アナログレコードの魅力が世界的に見直されている昨今。 アメリカやイギリスでも1980年代のレコード全盛期の生産量が30数年ぶりに更新されるなど各国でもその需要は高まっており、今日も新たなレコードは製造され続けている。 ところで、そんなレコードの製造に欠かせない「ラッカー盤」の製造を担うのが世界で唯一、日本だけということをご存じだろうか。
ラッカー盤とは、塩化ビニルのレコードに音を刻む際に使用するスタンパーと呼ばれる型をつくる一歩手前、最初に音を刻む工程で使用される円盤であり、かつて、アメリカのApollo Masters社とシェアを二分していたというが、2020年にカリフォルニア州にあった同社の工場が火事で全焼したことで、意図せず日本の工場が世界で唯一となってしまったのだ。
今回は、そんなレコードの源とも言える「ラッカー盤」を長野県で製造する「パブリックレコード」社の工場におじゃまし、全世界へと発送されるラッカー盤の製造工程を、社長である奥田聖氏のお話を伺いながら見学させていただいた。
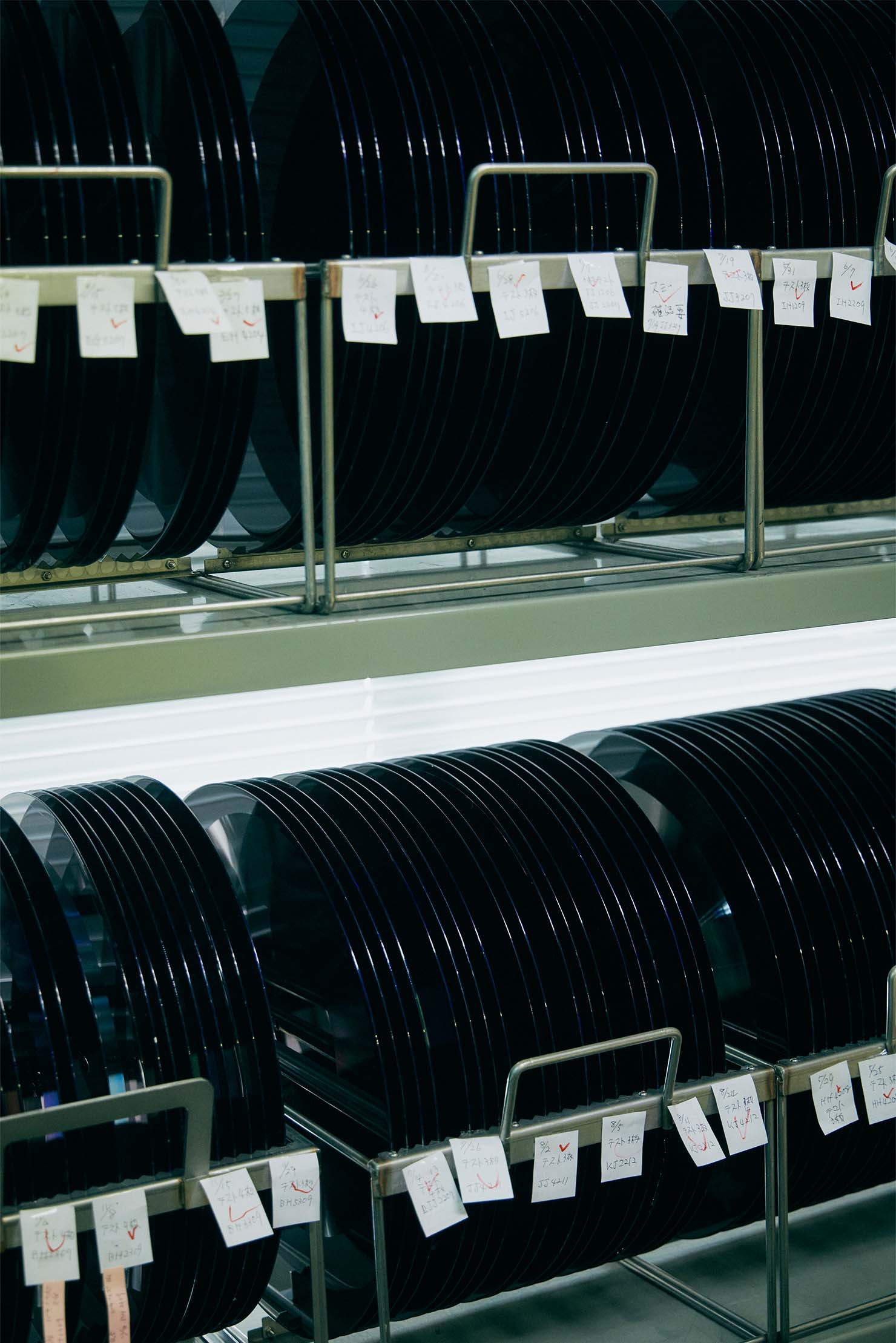
世界で唯一のラッカー盤工場
パブリックレコードの工場が世界で唯一、レコードの原盤とも言われるラッカー盤(=マスター盤)の製造を担っているということですが、まずは、アナログレコードの原盤となる「ラッカー盤」について教えてください。
ラッカー盤というのは、レコードの製造に欠かせない原盤であり、その名の通り、アルミニウムの芯盤にラッカー(=塗料)を塗装した盤になります。 そこにはじめて音を刻むことで、(一連の工程を経て)最終的に塩化ビニル製のアナログレコードへとプレスされた形で皆さんの手元に届きます。 つまり、ラッカー盤がなければ、(一部を除き)ほとんどのレコードは製造できないと言っても過言ではありません。
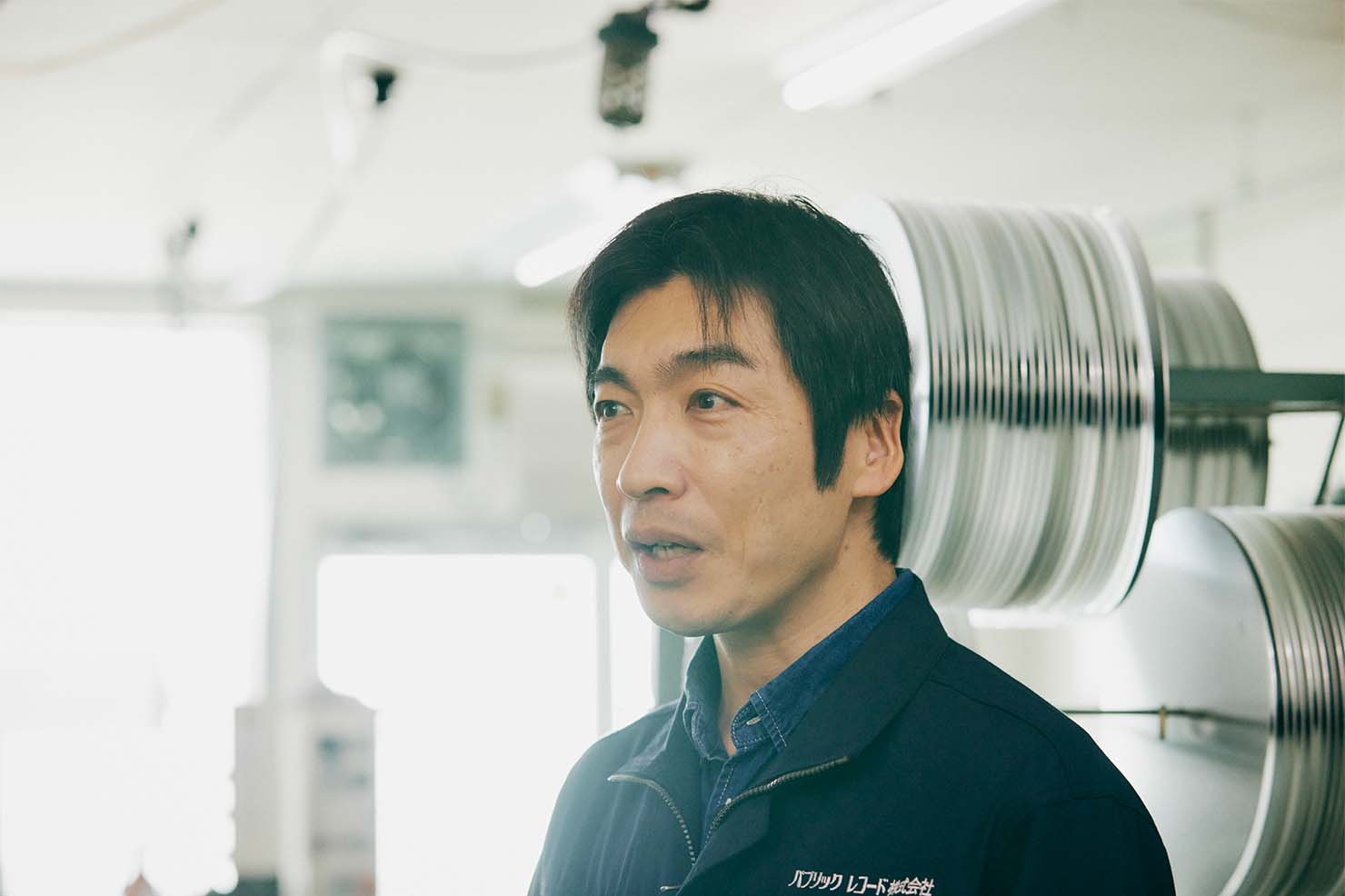
パブリックレコードは、1976年創業ということですが、これからCDの生産がはじまるという時代にラッカー盤の製造部門を立ち上げたのはどうしてですか?
私の義理の父(現会長)と祖父が、1982年に現在の規格となったラッカー盤の製造をスタートするのですが、当時はいまと違い、レコードが記憶メディアとしてすごく身近なものでした。 ピアノの発表会やカラオケの録音など、日常的な音を撮り溜めるメディアとして頻繁に使用されていたんです。 なので、日常使いでも使用される同じラッカー素材の録音盤製造も行っていました。 また、日本にマスターとして使用できるラッカー盤をつくっているところがまだなかったことから、国産化したいという想いで工場ラインを立ち上げることになったんです。 途中、時代の変化でカセットやCDが出てくるなか、「どうしてレコードなの?」と言われることもあったそうです。 当時、全世界に5社存在していたアナログレコードのラッカー盤製造工場ですが、次第に姿を消していきました。 アメリカに2社、フランスに1社、うちを含め日本に2社(1社はすぐに撤退)。 その後、アメリカの会社が合併し、フランスの工場が火事により焼失。 2020年にはアメリカの工場も同じく火事で焼失してしまい……。 いまや世界で唯一のラッカー盤工場になってしまったというわけです。
もはや手を引こうにも引けない状況……。 まさにレコード文化を担っているわけですね。
世界中から発注があると思うのですが、どんな国が多いのでしょうか?
当時から国内よりも海外からの発注が多かったのですが、なかでもヨーロッパの比率が高いです。 ここ数年は、アメリカの工場がなくなってしまったので、北米や南米からも注文をいただくようになりましたし、国内からの発注も増加傾向にはありますけど、香港、中国、台湾などのアジア市場からの需要も増えてきている印象です。
全世界で総体的に需要が増えているんですね。 若い世代を中心にレコードが見直されている状況については、どう考えていますか?
若い人たちの間では音楽は所有するモノではないのかもしれないですけど、モノが溢れている時代だからこそ、かえって大きくて不便なところが新鮮に目に映るのかもしれませんね。 ジャケットも大きいですし、部屋に飾ったり、コレクションしたくなるのではないでしょうか。 私としては、「モノとして残る」ところが魅力だと思っています。
昨年末に「第10回JASRAC音楽文化賞」を受賞されたそうですね。
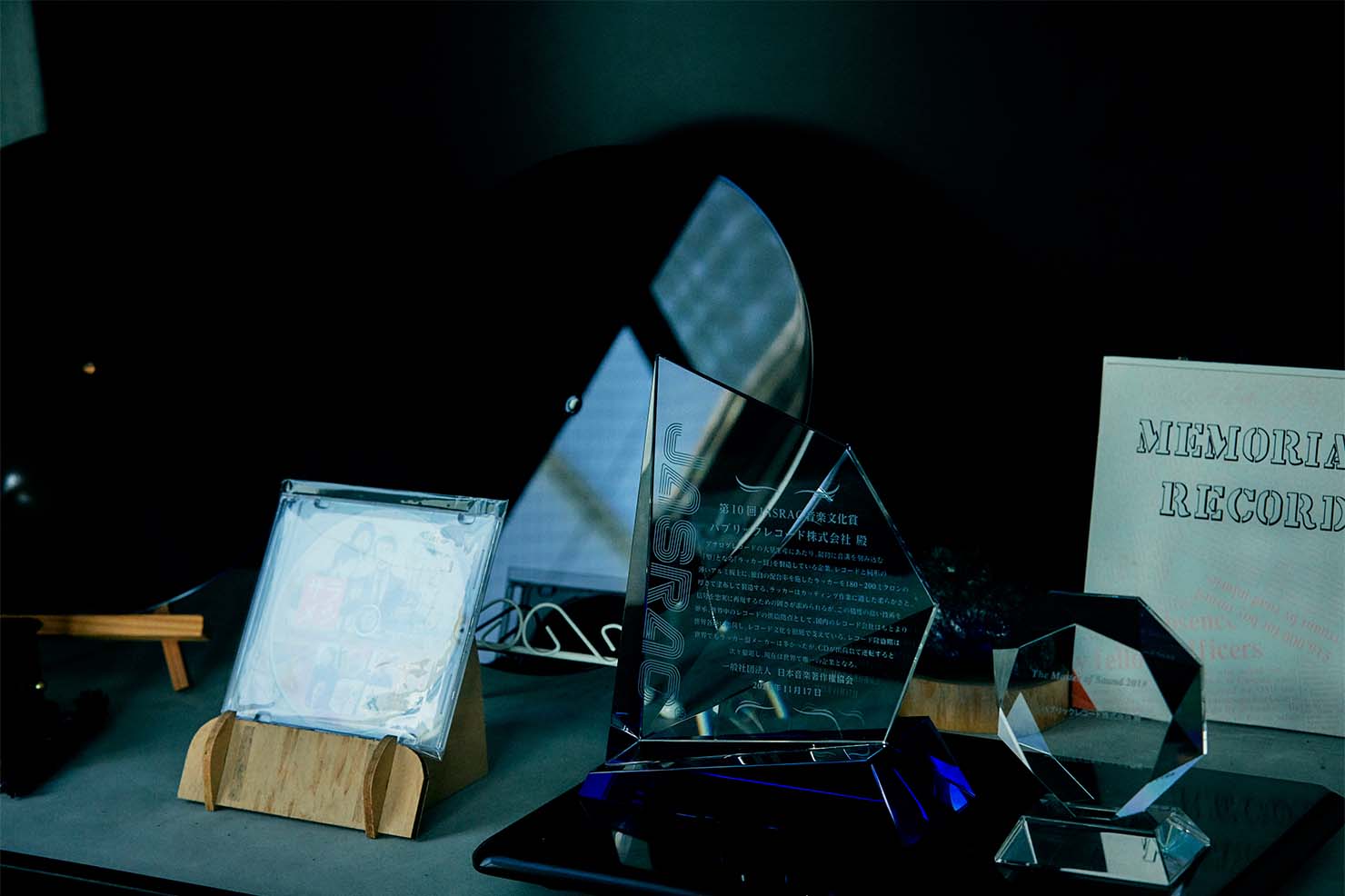
これまで、個人や団体の受賞はあったようなのですが、法人としては初なんだそうです。 担当の方が長野出身だったこともあったのですが、どういうわけか見つかってしまって(笑)。
世界で唯一となれば、いやでも見つかってしまいそうですね(笑)。
先ほども少しお聞きしたのですが、改めてアナログレコードの製造過程におけるラッカー盤の役割について教えてください。
まず、溝のない真っさらな状態のラッカー盤をレコード会社などが受け取り、ラッカー盤に音を刻んでマスター盤をつくります。 そのマスター盤にメッキをかけて型をとったものがメタルマスターという保存用マスターディスクになります。 そこからさらにメッキをとったものがマザー盤と呼ばれ、それを型どったものがスタンパーになります。 このスタンパーからプレスを行うことで、アナログレコードが生産されるわけです。 素材を変化させながら凸凹のコピー作業を繰り返してアナログレコードができているんですね。 その最初の素材になっているから “レコードの源” と呼ばれているわけです。
なるほど。 ラッカー盤からアナログレコードができるまでの一連の製造工程がよくわかりました。
スタンパーはプレスする度に消耗していくので、また新しいスタンパーをマザー盤からつくり、それを繰り返していくわけです。
ラッカー盤の品質管理というのは、その当時から確立されていたのでしょうか?
つくり方も材質もほとんど当時から変わっていません。 ラッカーに関しては、溝を掘った時の音に直接関わる部分なので、変化すると逆に困ってしまいますよね。 温度や湿度によって品質が大きく左右されるので、ラッカーが乾き切るまで注意深く管理しています。
堅牢性を兼ね備えた記録メディア
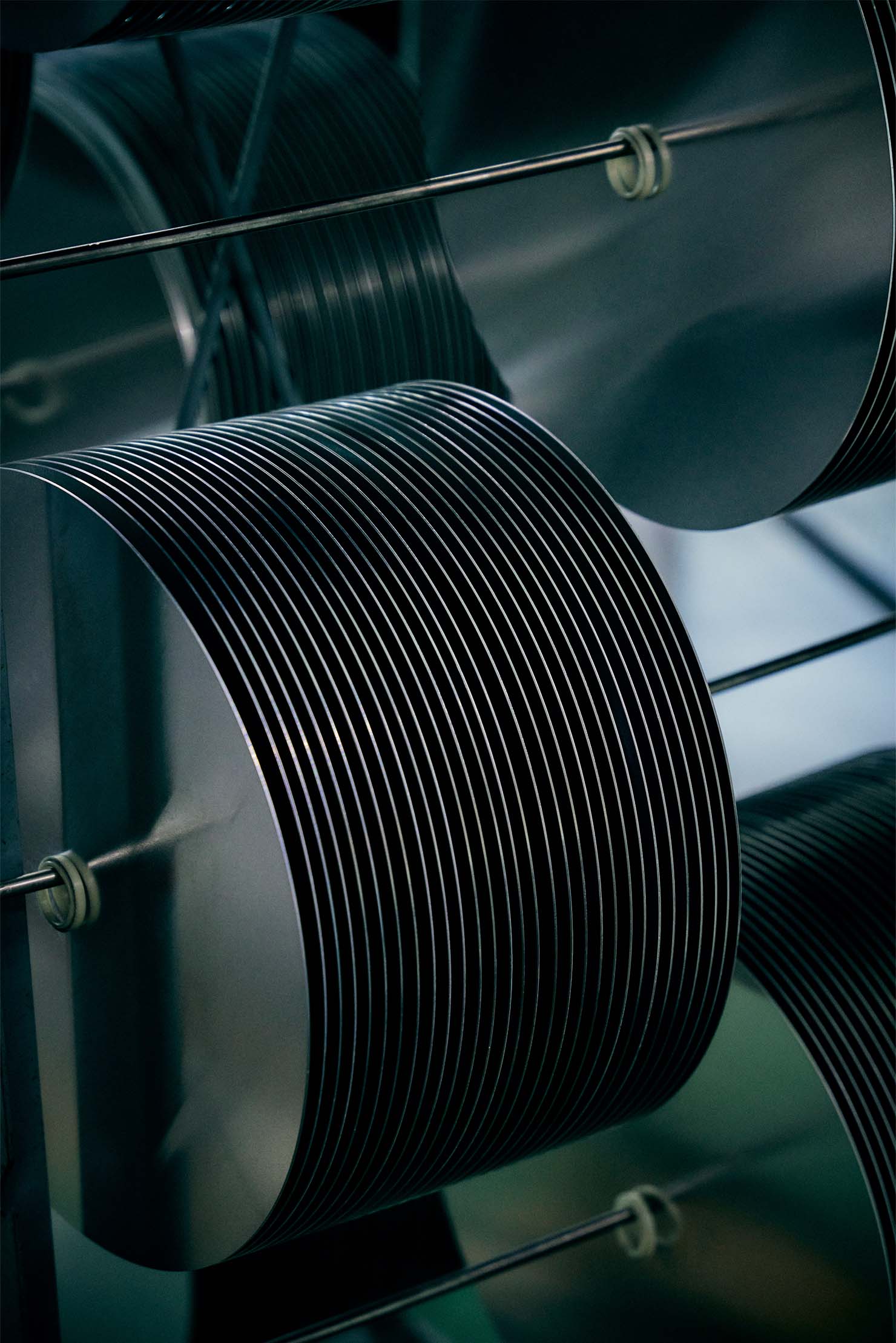
今後のアナログレコードの可能性については、どう考えていますか?
モノとしての記録メディアって、もう頭打ちじゃないですか。 音ならCD、映像ならBlu-ray、そこから画期的な進化がいまのところないですよね。 そういった形あるメディアにとって代わるようにサブスクのような定額サービスはあるにしても、レコードはこれからもまだまだ残り続けていくのではと思っています。
アナログレコードの面白さって、環境の違いで聴き手の印象が大きく変わることだと思うんです。 それがクラフト作品としての魅力のような気がします。
アナログレコードは溝が彫られた彫刻作品のようなものなので、針や盤質の変化で繊細に音も反応するんだと思います。 データだと壊れてしまったらそれで終わりですけど、アナログレコードは多少削れても聴くことができますし、情報を残すメディアとしての堅牢性は高いと思っています。 工場では、10インチ、12インチ、14インチのマスターとしてのラッカー盤を生産しています。
というところで、工場内を見ていきましょうか。
「変わらないこと」が支えるレコード文化
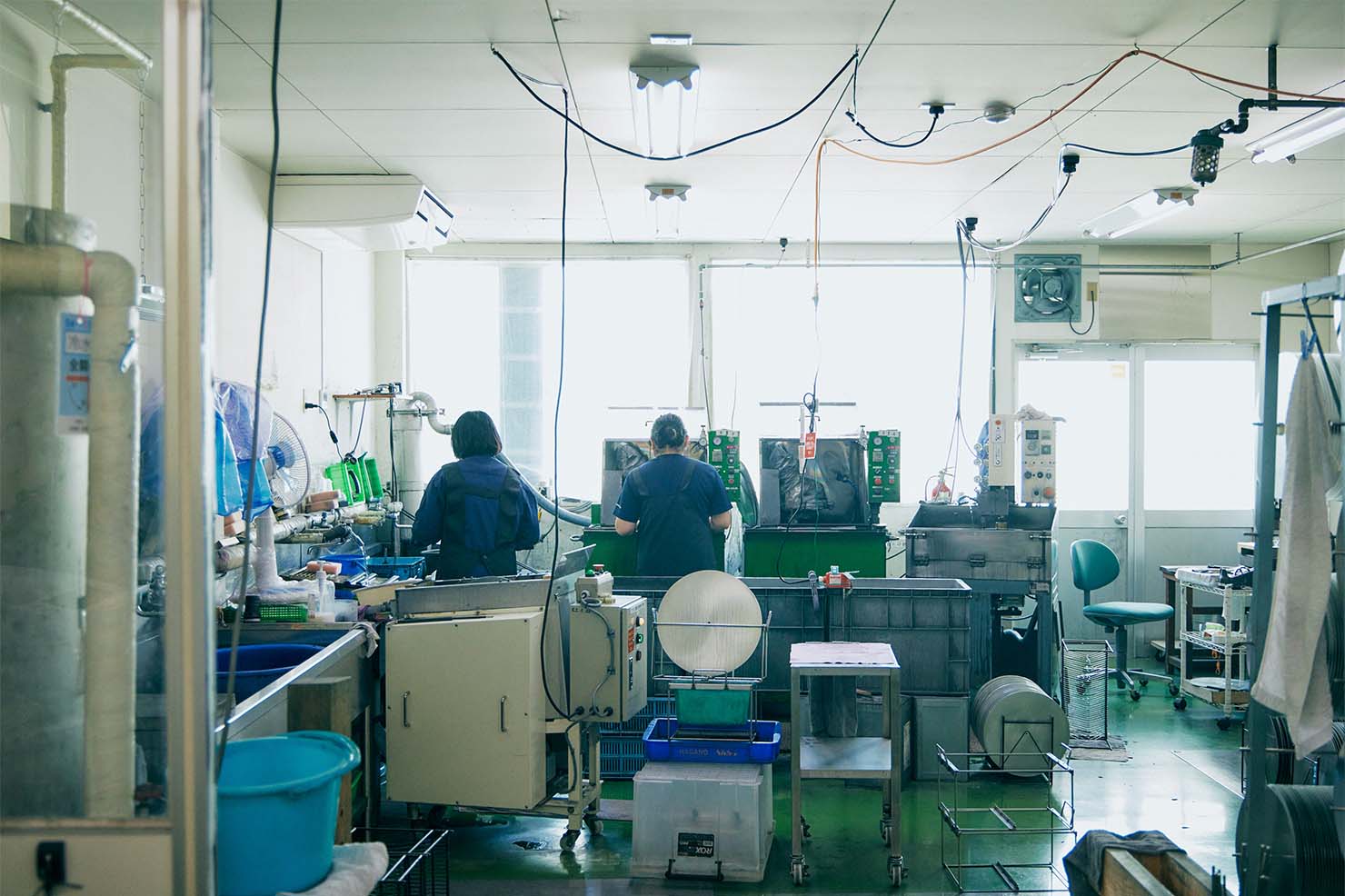
工場内には、アルミニウム製の原盤を研磨する部屋、塗装前の盤の品質を検査する部屋、そして、ラッカー塗装する塗装部屋があります。 まずは、アルミニウムを研磨する部屋から見ていきましょう。
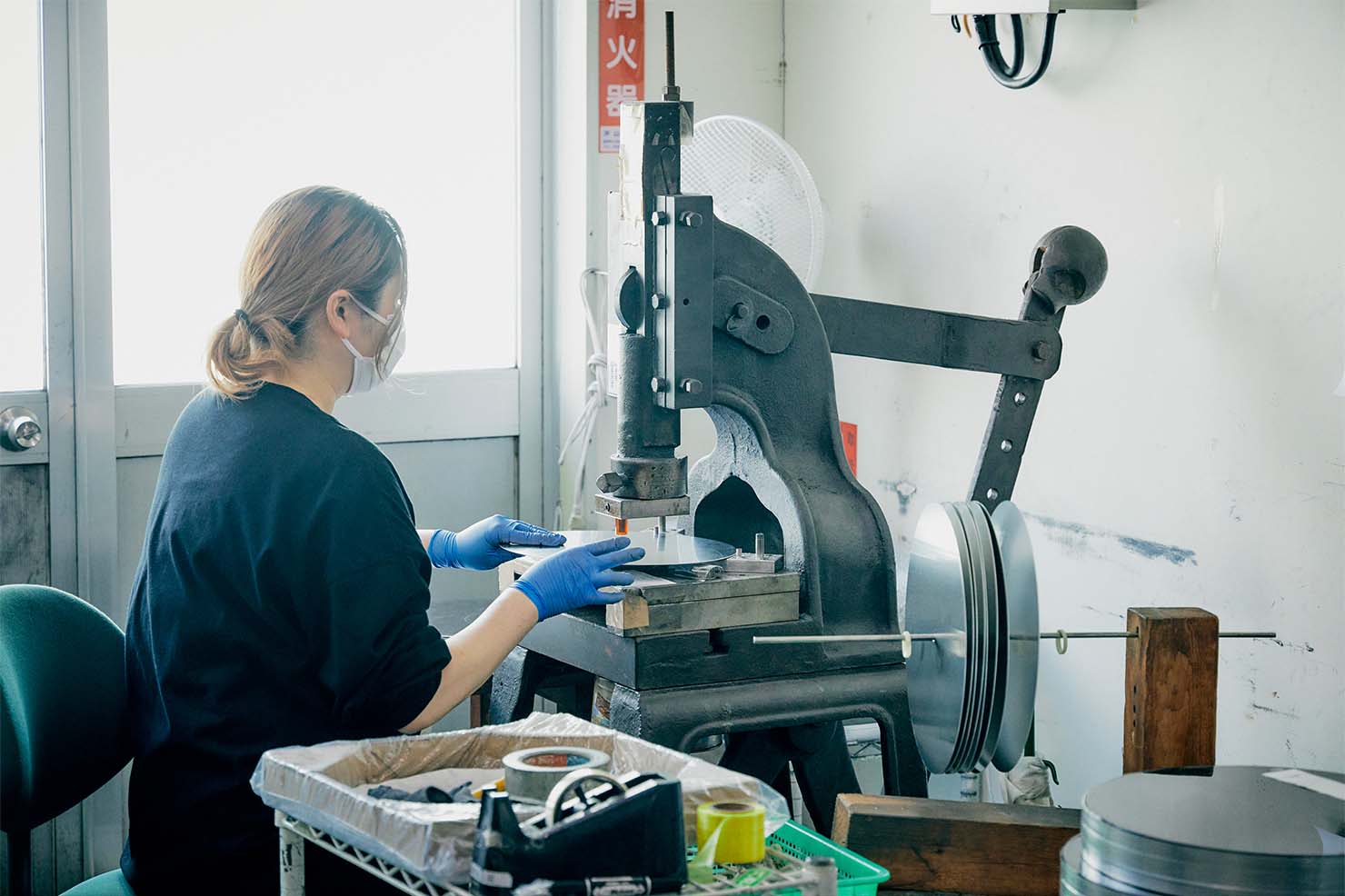
この部屋では、塗装前の盤の状態を整える作業をしています。 センターホールを空けたり、アルミニウムの表面についた汚れを落とすために溶液に浸けたり、凹凸を滑らかにするために研磨機で研磨し、240℃の熱でプレスしながら表面を平にしていきます。
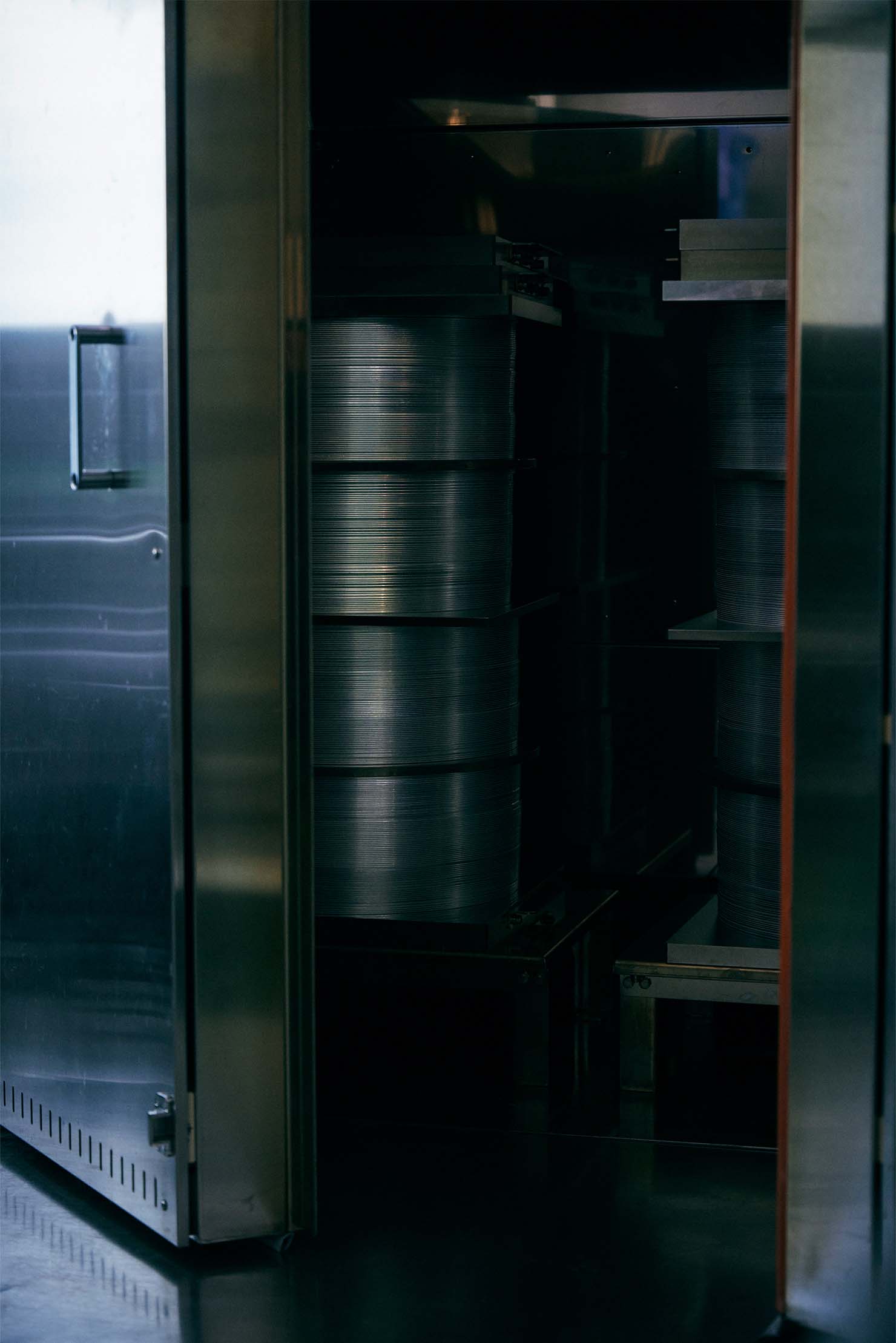
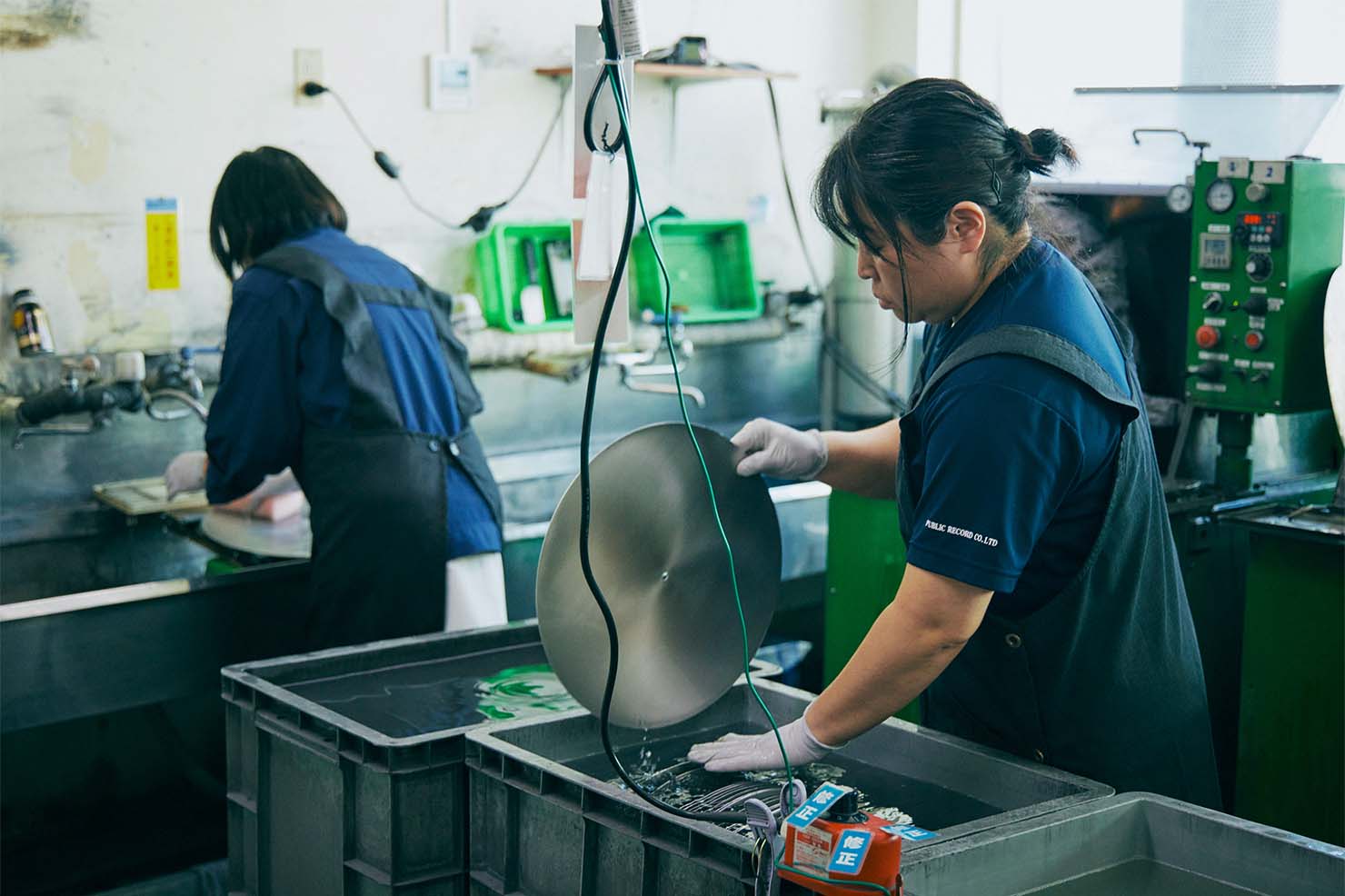
研磨を終えたら、次はクリーンルームへと検査にまわします。 クリーンルームで検査員のチェックに漏れた盤は、再びこの部屋に戻ってきて再度研磨にかけられます。
クリーンルームへは入れるのでしょうか?
残念ながら検査員以外はクリーンルームに入れないんです。 小さな埃でもノイズになったりと、音に直接影響が出てしまうといけないですし、埃が入らないように最新の注意を払っています。 人の体温でも温度や湿度が変化してしまうので。
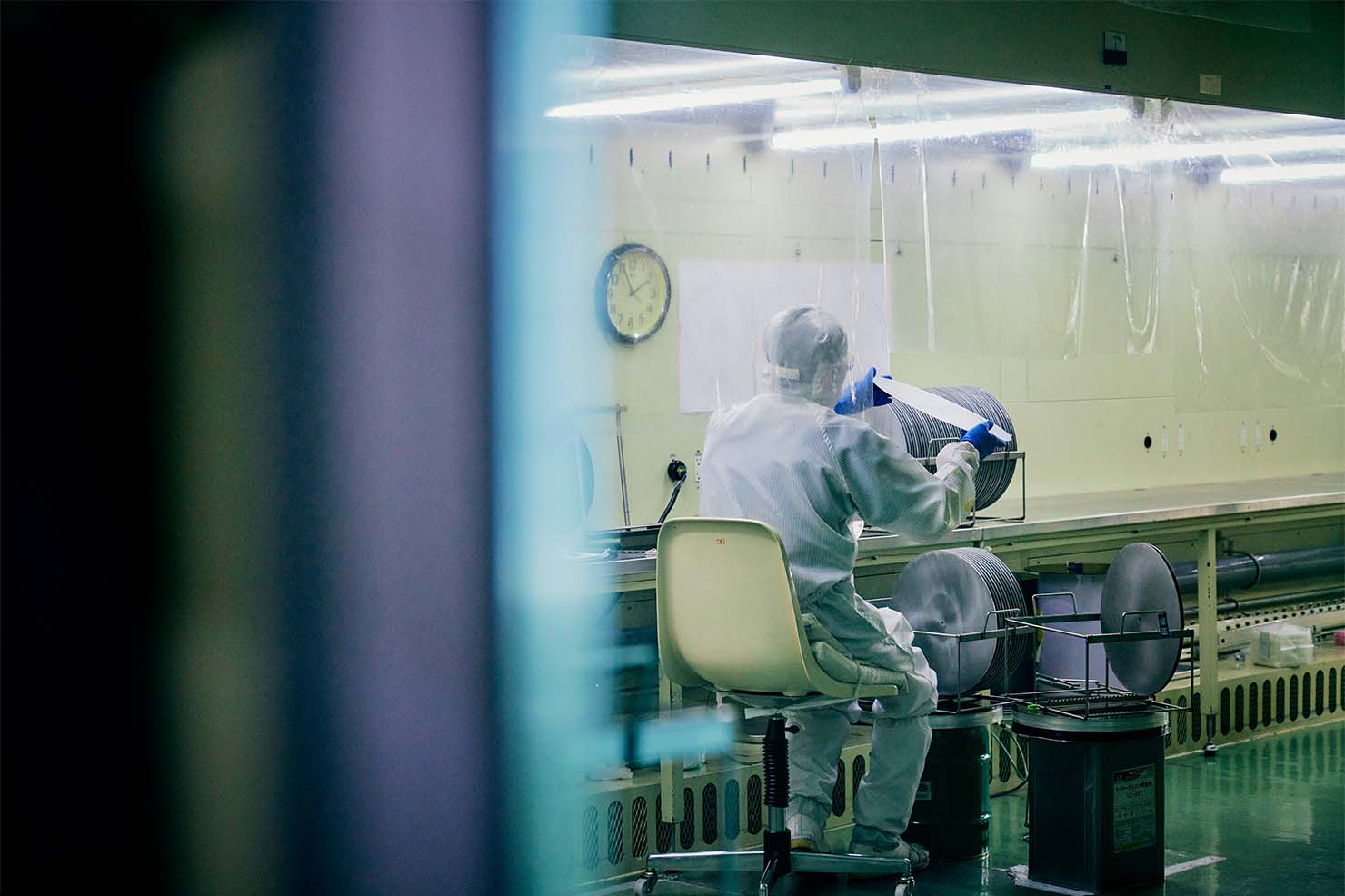
クリーンルームの検査をパスしたものは塗装室へとまわされます。 塗装は、基本的に3人1組。 塗装前の盤をベルトコンベアーへ載せる人、カーテンのように落ちてくる塗料を潜り塗装された盤をとり上げる人、そして、台車を動かしたりと2人のフォローをする人で構成されています。
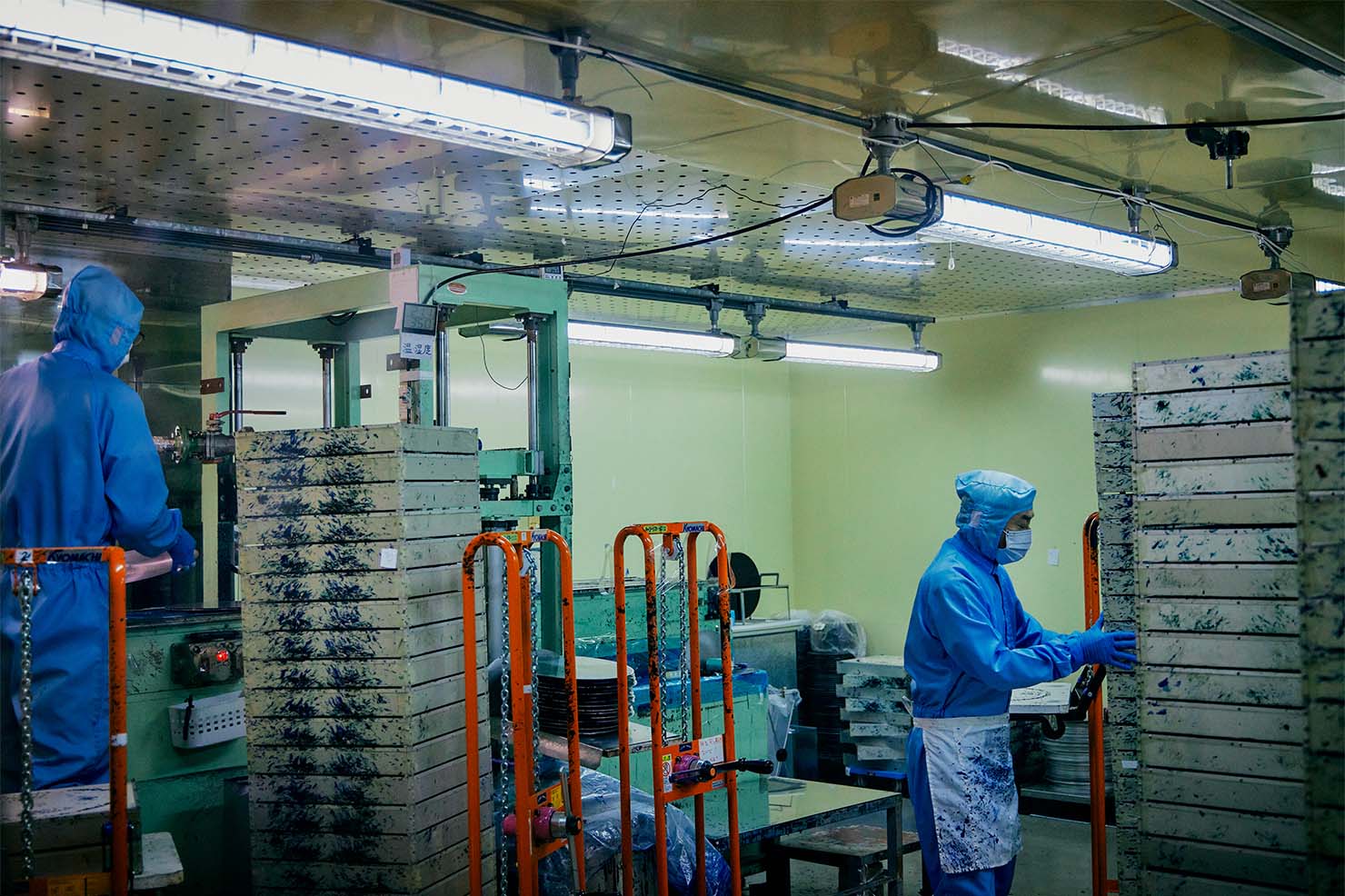
塗装には、どのくらいの時間を要しますか?
塗装は両面しなければならないので、午前中に片面を塗り、それを一日乾燥させてから、次の日の午後に裏面を塗装して仕上げます。 なので、一枚の盤を塗るのに丸2日かかるということです。
塗料を塗ったあとに埃がつかないように、すぐに箱に収めて乾燥させていますね。 流れるような作業で手についた塗料が箱にサイケデリックな模様をつくっています(笑)。
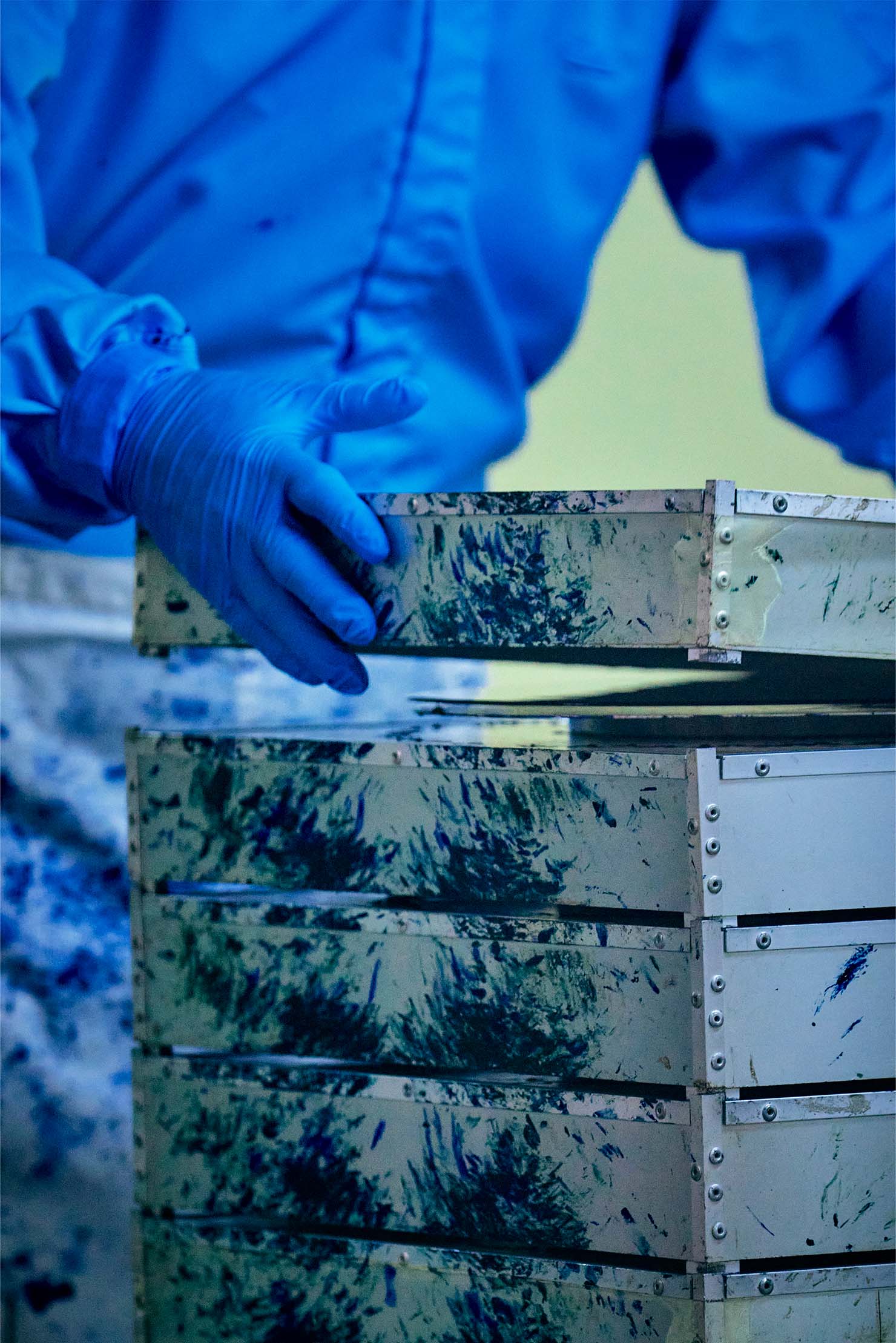
塗料は以前から変わらない配合でフィニッシュされているのでしょうか? よく見ると、黒ではなく、青紫っぽい色なんですね。
配合を変えてしまうと音が変わってしまうので、今でも当時と同じ配合で塗料をつくっています。 溝を彫れる柔らかさと形状を維持する硬さを共存させないといけないので、当時は随分と研究を重ねてつくっていたようです。 温度や湿度によっても変化するので、外的要因から影響が少ない配合になっているんです。
当時と比較して、ラッカー盤の生産量に変化はありますか?
現在の一日あたりの生産量は、80年代後半のピーク時と一緒です。 というのも、スペースや塗料タンクの量が限られているので、どうしても一日につくれる量に限界があるんです。 あとは土日もフル稼働にするかどうかというぐらいで。
塗装を終えたラッカー盤を出荷するまでに、どんな検査があるのでしょうか? リスニングルームには、カッティング用の機材も設置されているようですが。
検査室で最終的な検査をして、それをクリアした盤は2日間ほど自然乾燥させ、さらに乾燥機で強制乾燥にかけてから25枚の束を2セットで梱包し、一箱にまとめて出荷します。 ちなみに、リスニングルームでは音の溝を彫るのではなく、盤に問題がないかを検査するためのテストカットを行っています。 きれいに彫れるかどうか針を入れて切れ味を確認するのがメインですが、そのあとにノイズの確認も行っています。 ノイズは無音でないと聴きとれないので、無音のまま、昔のレコーディングスタジオには必ずと言っていいほど置いてあったALTECのスピーカーで、針が通る音だけを通常聴く音量よりもさらに音量を上げて検査していきます。
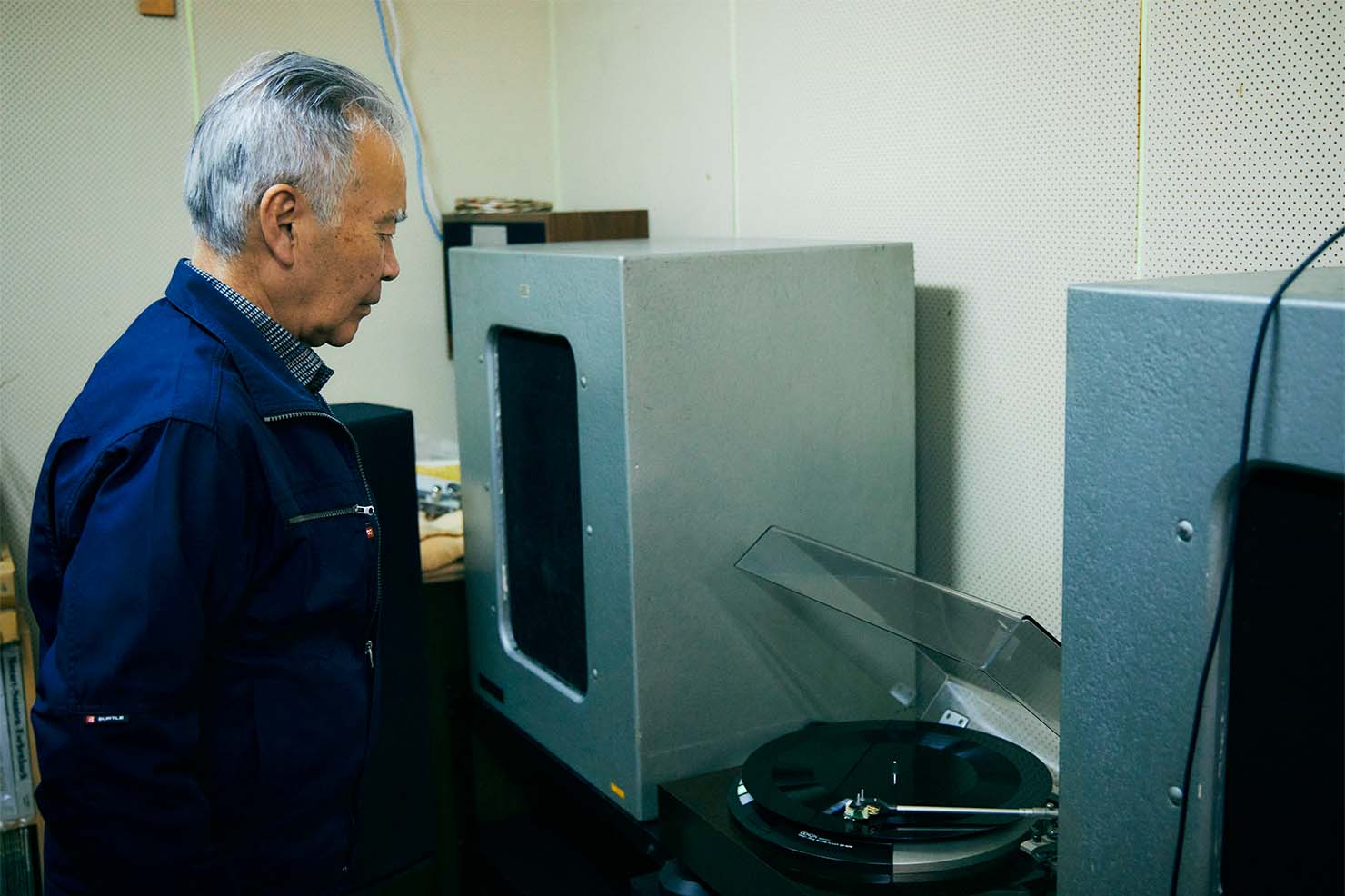
東洋化成さんの工場でも同じようなカッティングマシンを見たことがある気がします。
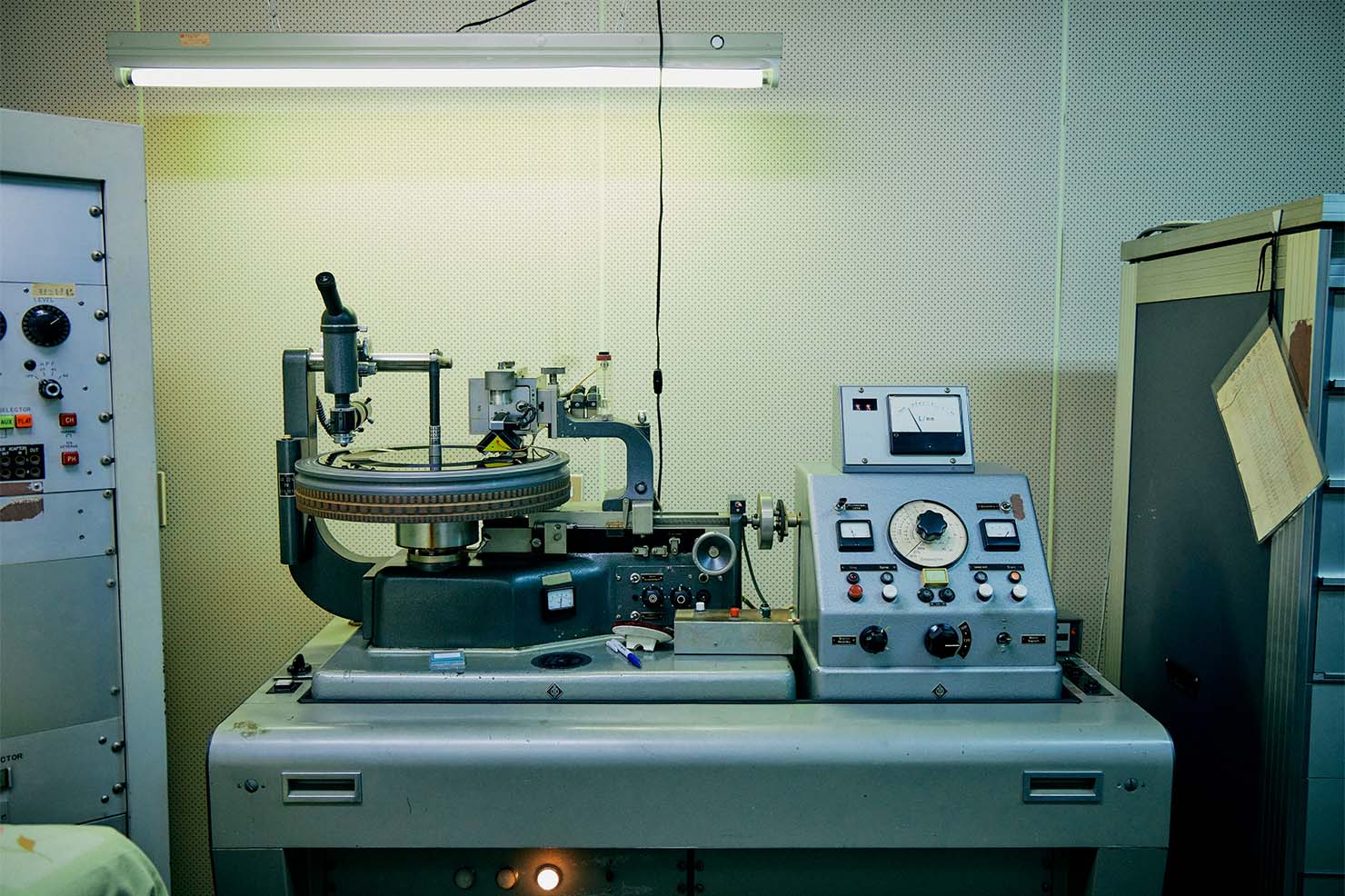
そうですね。 おそらくこの機材よりも一つ新しい型だと思います。 ドイツ製のNEUMANNのカッティングマシンで、もう製造されていないので、貴重なものだと思います。 レンズを覗くと一定の間隔で溝が彫られているのがわかると思いますが、本来は無音ではなく音を入れるので、もっとウネウネとした曲線を掘っていきます。 いま見ていただいている溝の幅は、大体70ミクロンほど。
実は、カッティングに使用する針をつくっているのも、日本に一社しかないんですよ。 Orbrayという会社なんですけど。
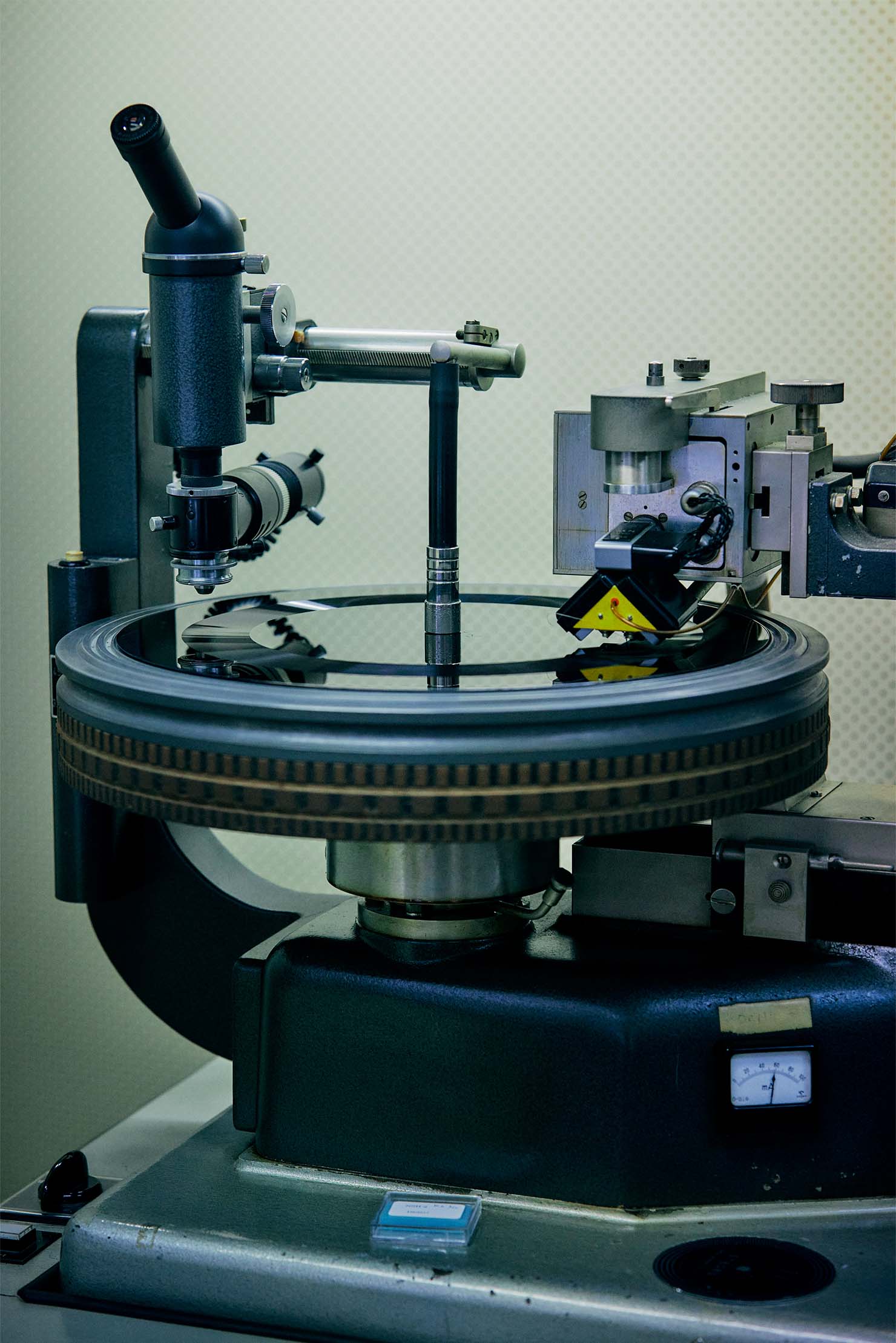
レコードを取り巻く状況がこんなにも日本に支えられているだなんて、思ってもみませんでした。 一方で、何かもっとレコード文化をサポートするような取り組みが必要な気もしてしまいますね……。
もし、ラッカー盤がなくなったとしても、DMM(=Direct Metal Mastering ラッカー盤を用いずにマザー盤を製造する方式)があるのでレコードの生産がゼロになることはないと思います。 それこそ、チェコとかドイツではそういった技術を使って製造していますし。 ただ、大半の製造はラッカー盤を使用しているのが現状ではあります。
ところで、パブリックレコードという名前の由来についてなのですが。
先代が名づけた当時はまだラッカー盤は完成していなかったんですけど、パブリックがもつ「公」という意味の通り、「みんなのための記録」ということです。
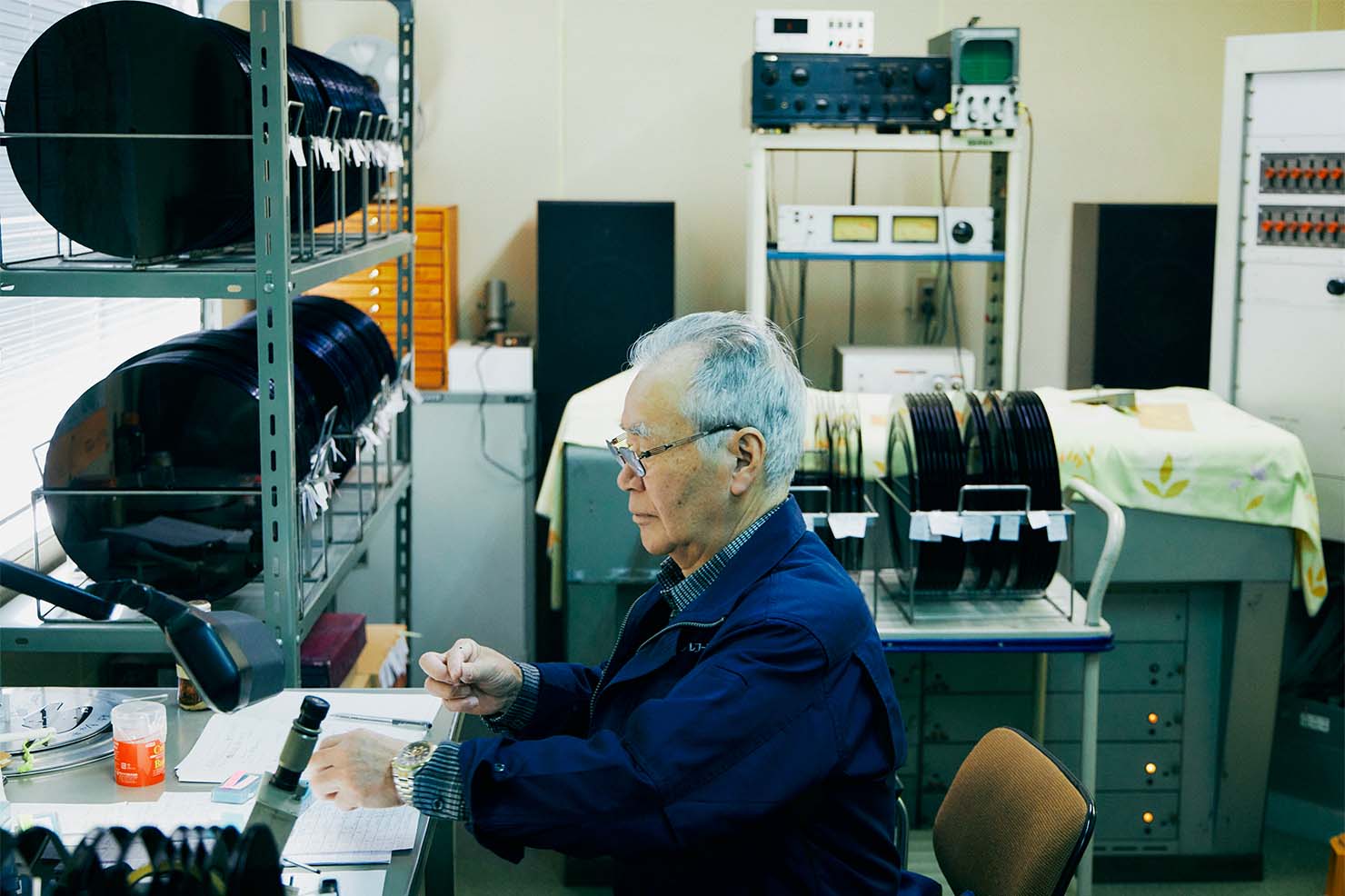
先ほども少しお話しいただきましたが、パブリックレコード立ち上げ直後にCDが台頭しはじめ、レコードが衰退する時期とも重なると思うのですが、なぜラッカー盤の製造を続けられたのでしょうか?
当時、アナログレコードは日本から完全に消えたと言っても過言ではないのですが、ヨーロッパではまだ若干ニーズが残っていたので、そのために続けようという先代の判断でした。 でも、その時は本当に辞めてしまおうか悩んでいたようなんです。
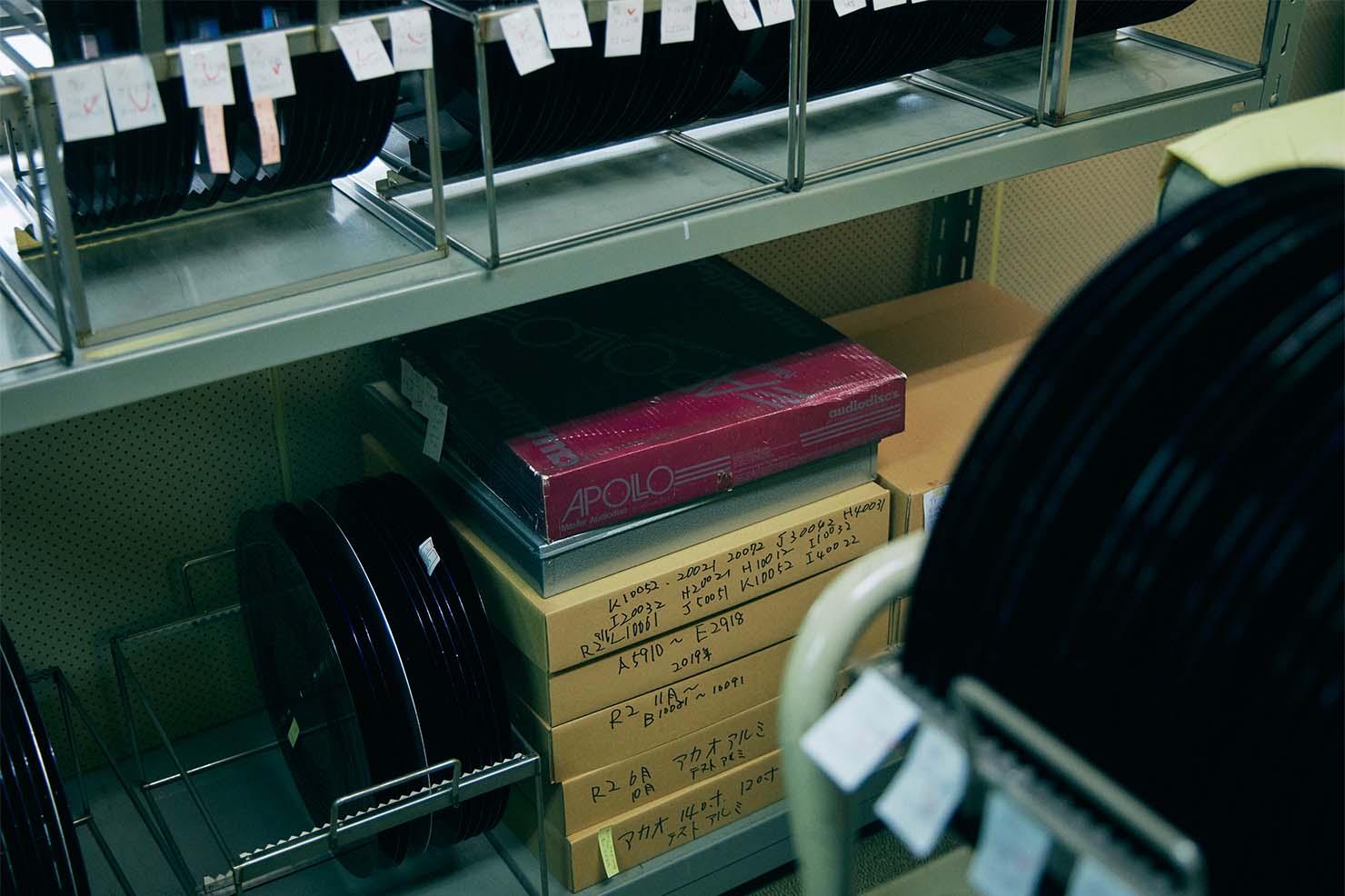
最近は、アナログレコードで音源を残したいというアーティストの反応も一定数あるようです。
既にマスター盤の型があれば再度プレスできますが、これから新たにアナログレコードをつくるアーティストさんは、ラッカー盤から音を彫るところからはじめないと作品をつくることができない。 そう言う意味でも、責任重大ですよね。
いまや世界で唯一の工場となってしまいましたが、やはりプレッシャーは感じていますか?
やはり供給責任は強く感じています。 途絶えさせてはいけないな、と。 でも、こうやってレコードの存在をまずは知ってもらって、レコードをもっと身近なメディアとして認識してもらうことができれば嬉しいですね。 テープ以前の時代には、身近な記録メディアとして日常に存在していたレコードですし、録音盤も多くの企業が製造していた。 レコードを再び身近な存在にするためにも、私たちは品質を維持しながら、これからも全世界にラッカー盤を供給し続けたいと思っています。
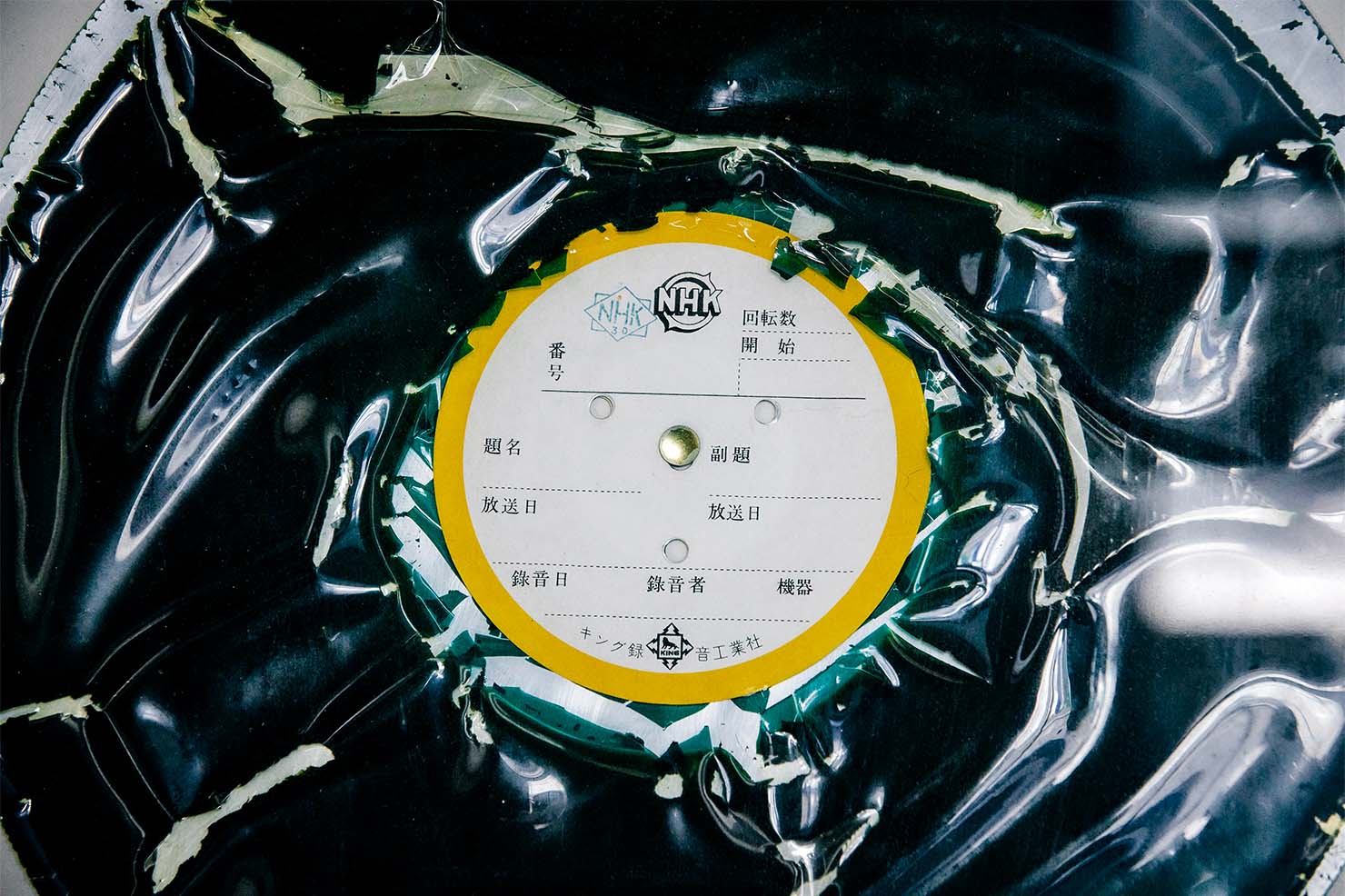
Photos:Shintaro Yoshimatsu
Words & Edit:Jun Kuramoto(WATARIGARASU)