アナログ製品に限らず、ひとつの製品には多くの人が携わっている。 たとえば野菜の直売所にいくと、そこに並ぶ野菜にはプロフィールが書いてあり、産地や生産者の顔を見ることができる。 作り手の顔が見えると、その野菜がここに届くまでのストーリーが想像できて、なんだか「温かさ」を感じる。
イヤホンやマイク、ヘッドセットなどさまざまな音響機器を製造販売しているオーディオテクニカ。 その歴史はアナログカートリッジの製造・販売からスタートし、創業の1962年から現在まで多くの製品を展開してきた。 この連載ではその作り手にフォーカスを当て、バックストーリーを発信していく。
今回は製品の生産・納期管理、生産ラインで使用する治工具類の準備やメンテナンスによる作業改善を行っている生産部生産課の髙橋 譲に話を聞いた。 これまでに携わってきた製品は、『AT-ART1000』、業務用マイクロホン、そして直近では『AT-ART1000X』の生産を担当。 学生時代に活動していた演劇部で経験したPAの話、オーディオテクニカに入社するまでに感じていたこと、そして現在の仕事のことまで、アナログを紡ぐエンジニアのストーリーをご紹介しよう。
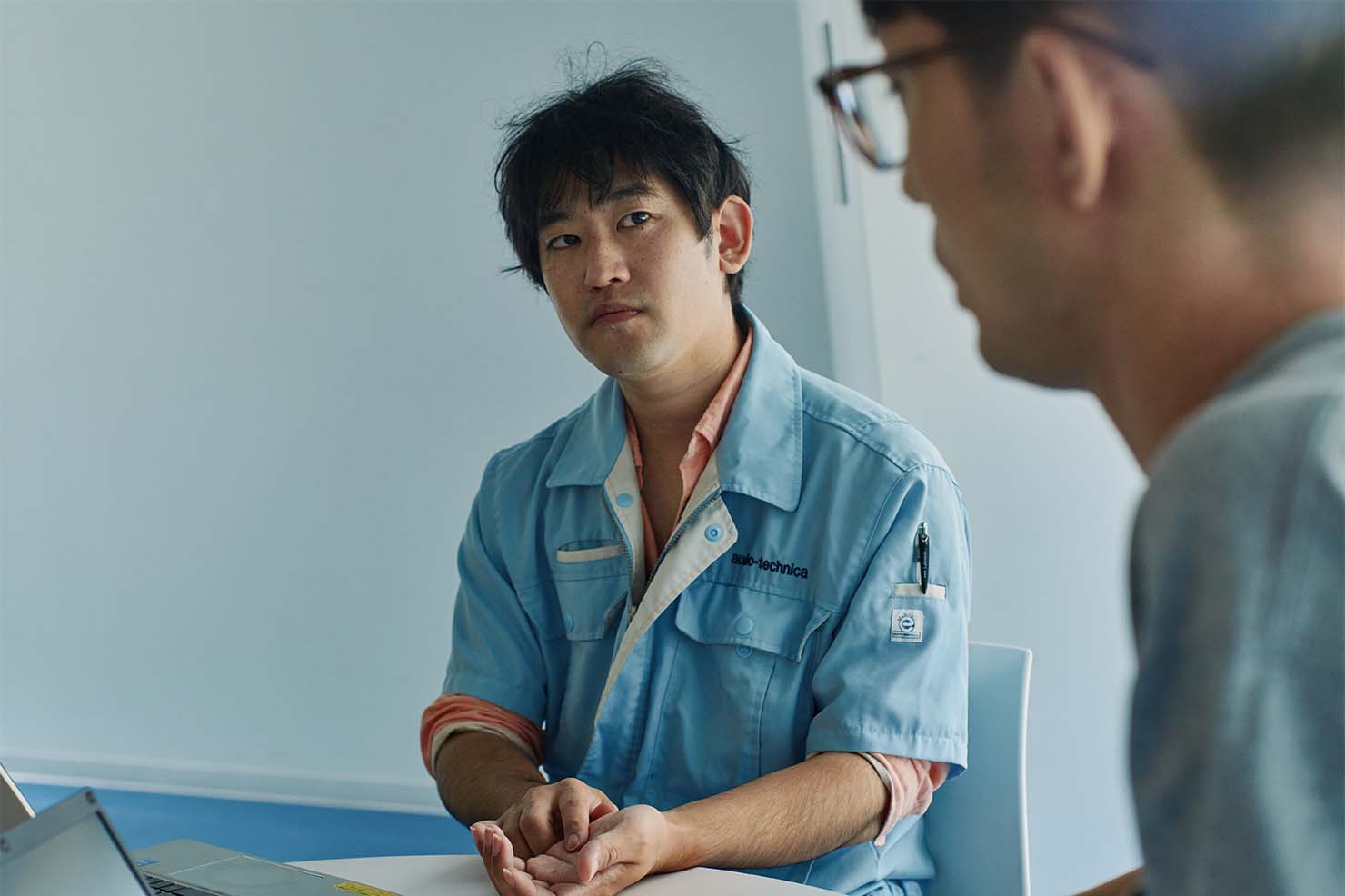
大学時代、演劇部でのPA経験
髙橋さんが音響機器に興味を持ち始めたのは、大学時代に所属していた演劇部での経験がきっかけということでしたね。
そもそも演劇部に入ろうと思ったのは、舞台という大がかりなものを組み立ててみたいという気持ちがあったからです。 そして、部活の説明会の時間で話を聞いているうちに、音響チームに興味を持つようになり、そこで簡単なPA作業をするようになりました。
オーディオテクニカを知ったのもその部活動が少し関係しているとか。
「この製品を使っていたから!」といった濃いエピソードではないのですが、部活で必要なマイクケーブルを当時探していて、たまたま店頭で見つけたケーブル付属のハンドマイクがオーディオテクニカのマイクロホンでした。 たしかVDシリーズだったような気がします。
今思えばこれが私のオーディオテクニカとの出会いでした。 ただ、当時は何の気なしに手に取っていたので、就職活動のときは社名にピンときてはいませんでしたね。 そこからさまざまな企業をみていきましたが、最終的に音響機器を専門に入力から出力まで幅広く開発・製造を行っていた点が決め手となり入社しました。
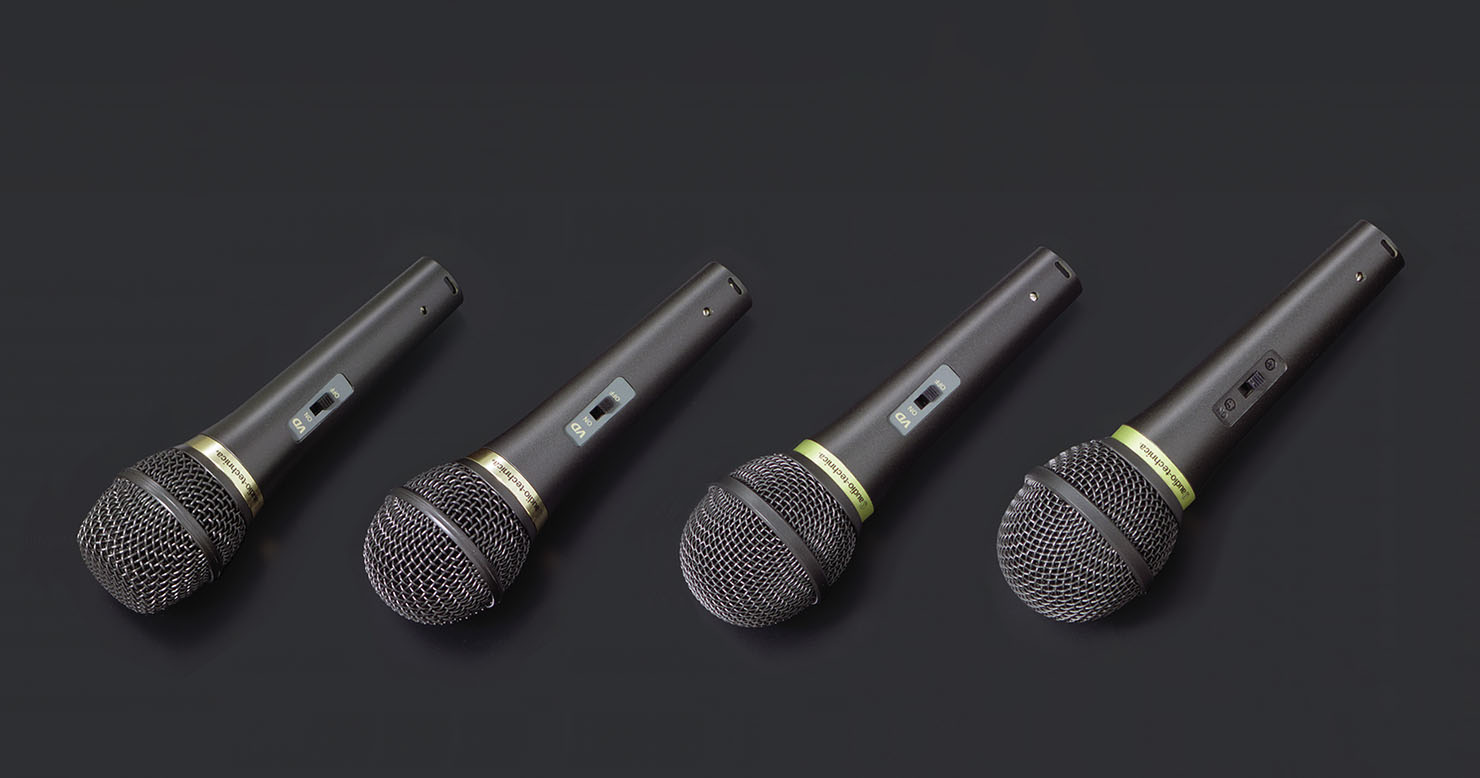
今年で入社して11年目になるようですが、当初はスピーカーの開発に関心があったそうですね。
はい、自分で開発してみたいなと。 ただ、実際のところは音響機器を取り扱えるならどこの部署でも関心をもって取り組めると思っていましたね。 入社後の配属先はマイクロホンの製造技術開発を担当する部署でした。 マイクロホンは学生時代に舞台の音響周りを担当していたこともあり馴染みがあるカテゴリです。 そこから3年目になると入力機器に縁のあるカートリッジの業務に携わるようになり、そこで担当したのがAT-ART1000でした。
そして技術開発の部署から生産の部署へ異動、今も変わらずマイクロホンやカートリッジを担当しています。 カートリッジは直近だと、7月に発売されたフラグシップモデルAT-ART1000Xを手がけました。 生産部は主に技術開発部門と協力して生産設備や治具類の準備、作業指示書の作成など行う「製造技術課」と、注文が入った製品を納期通りに進行するためスケジューリングし、生産、さらにラインの整備を行う「生産課」の2つのグループで構成されています。
*治具:製品の組み立てをしやすいようにサポートする置台や追加工を加えた工具類のこと。
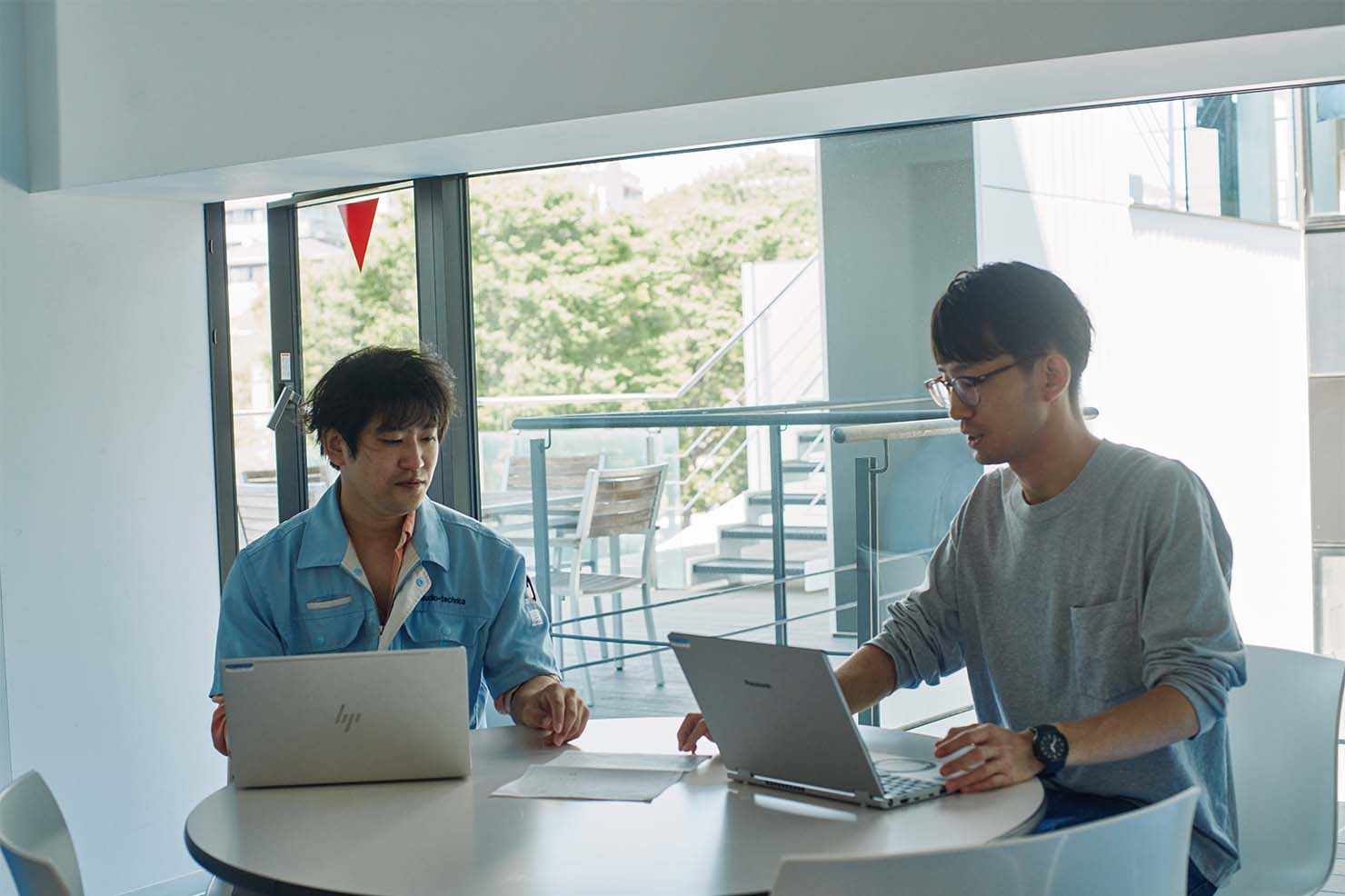
顕微鏡での作業、集中力との闘い
ここからはそのART1000Xについて、発売までのお話を伺いたいと思います。 本製品は “コイル” が重要だと聞きましたが、生産課の髙橋さんが担当する工程でのこだわりや工夫を教えていただけますか?
製造的な観点でいうと、コイル周りの工程がこだわりです。 コイルは関係部署の協力によりきれいな状態に巻けるようになり、その先は極力性能に影響しないようにコイル線をカートリッジ背面端子まで配線・処理しています。 サイズが小さいので常に顕微鏡を使用しての作業で集中力との闘いとなり、工具類も加工を行い作業性を向上させて短時間で完了できるよう工夫を凝らしています。
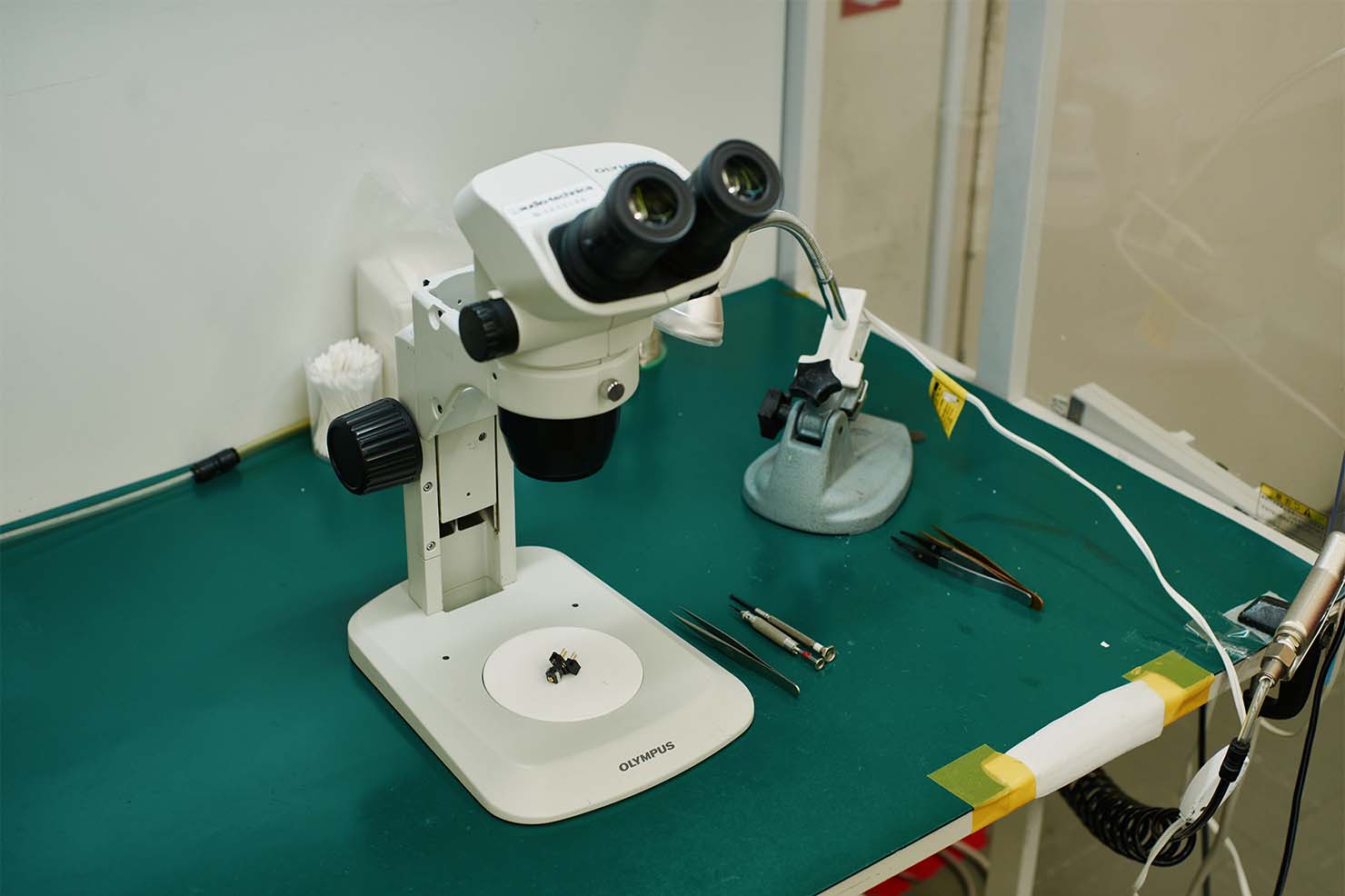
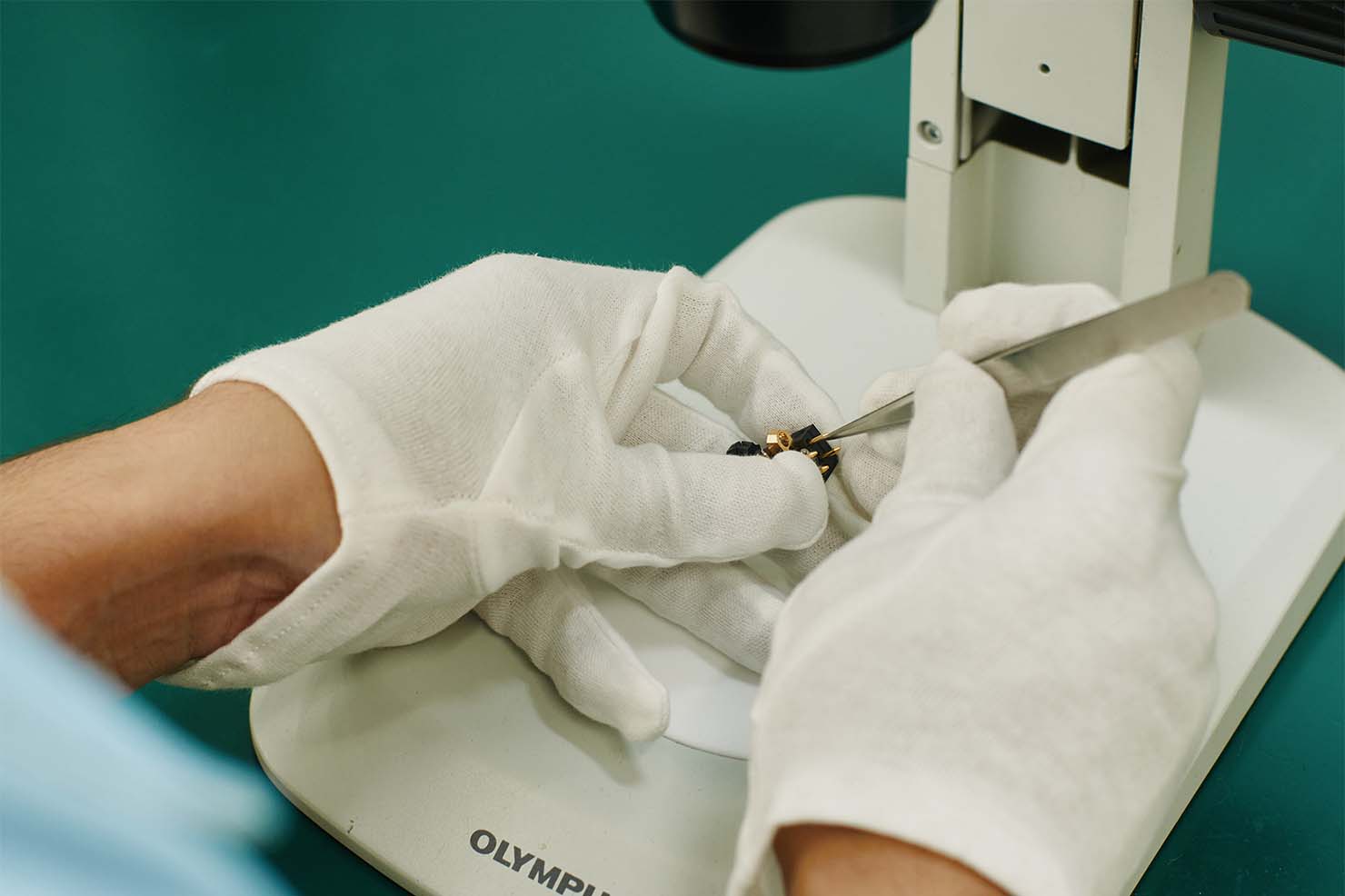
カートリッジ自体がものすごく小さなものなので、そのパーツとなるとさらに小さいですよね…製造において最も苦労したポイントはどういったところでしょうか。
苦労したことは「治具の作成」、「工程の確立」の2点だと思います。 私自身は治具自体の作成は行っておらず、製造技術課で治具を準備してもらいます。 それを実際に使用し情報をフィードバックして治具の改善を行っていただき、設計者と相談して巻き方の工程(順番)を確立していきました。 この工程は開発部門のこだわりもある工程ですので計画日程のギリギリまで様々なパターンを検討して時間を多くかけたところです。
全体としては、技術チーム→製造技術チーム→生産チームという流れで進んでいきます。 技術チームで設計・開発を行い、製造技術チームが情報を共有して生産できるように手順通りに仕様を満たす製品を組立・梱包していく、といった流れになります。
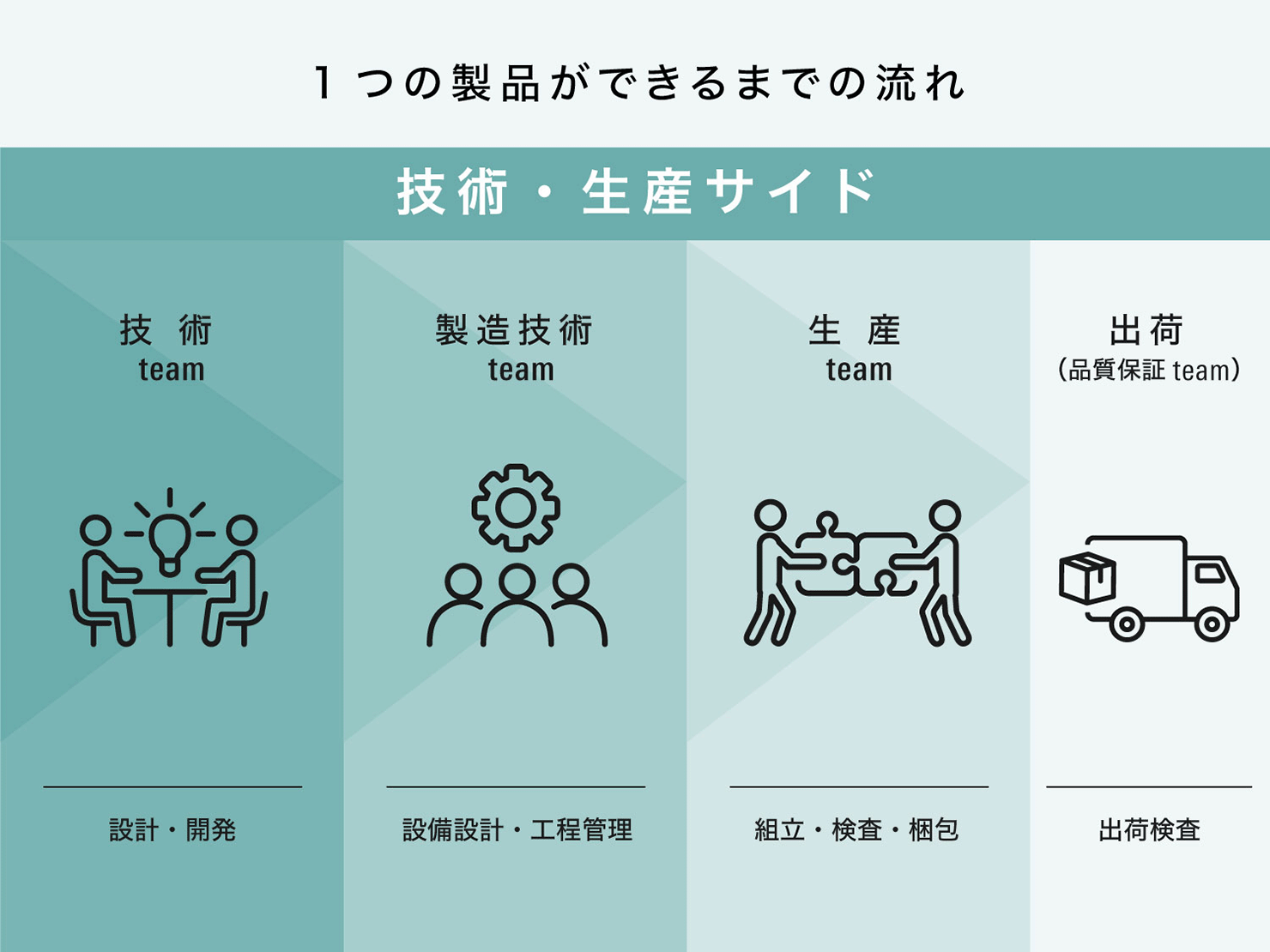
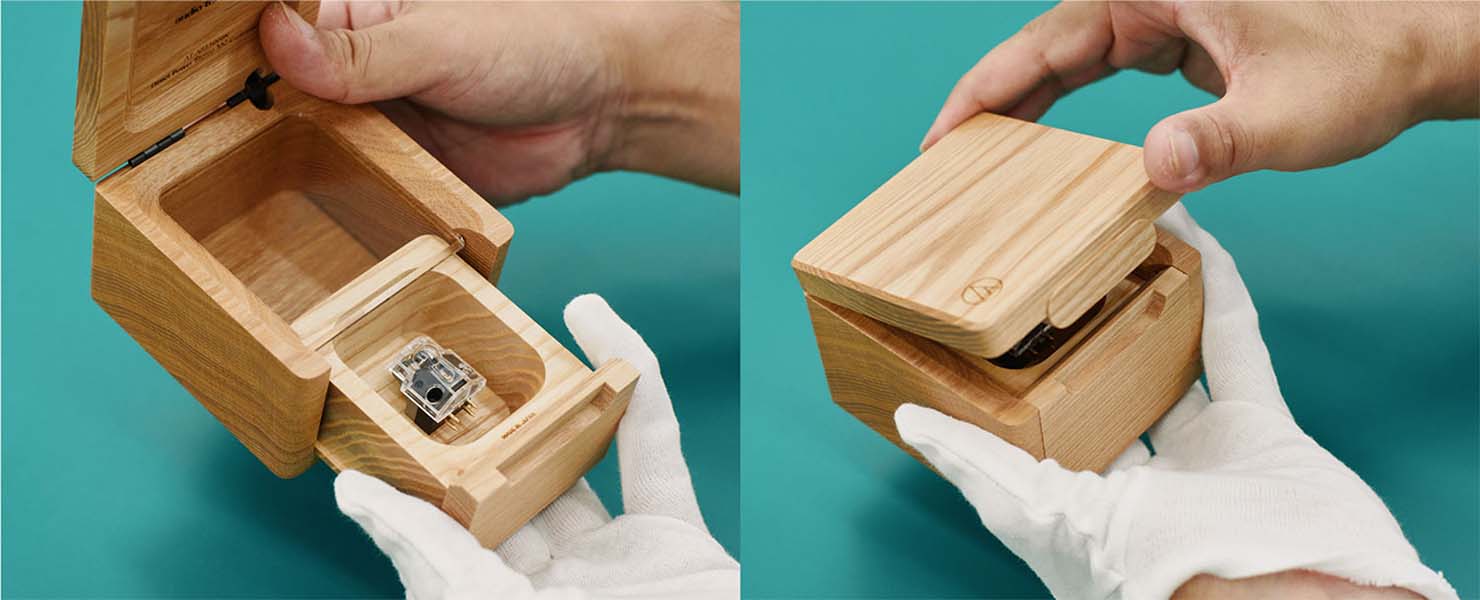
手先はもちろんですが、頭も使うので相当な集中力が問われそうですね。 作業中の息抜きルーティーンなどありますか。
どうしても顕微鏡を使用しての作業となるので、長時間の作業が難しく集中が切れることがあります。 その状態で作業を続けると完成状態や仕損じを増やすことに繋がりかねないので、そんなときはコーヒーを飲んだり、他の業務を行い時間を空けたりしています。 そうすることで集中力を戻しています。
トランスデューサーメーカーであること
創業時から作り続けているカートリッジ。 髙橋さんはそのフラグシップモデル担当されていますが、オーディオテクニカだからこそできると感じるのはどういったところでしょうか。
”音を維持したり、逆に変えていくこと” が続けられることだと思っています。 製品のカテゴリにもよりますが、たとえば弊社の代表的な製品であるVM型カートリッジのように、初代モデルが1967年に発売されてから20年以上進化させながらも変わらず生産しているものもあれば、有線からコードレスのBluetooth対応モデルが登場したヘッドホンやマイクロホンのように時代の変化やニーズに合わせてその形を変えていくものもあります。 その両方が出来ているのは、自社内でコア部分のトランデューサー(音を拾ったり出したりする部分)の設計生産していることが大きいのだと感じています。
自分の今後の目標として、トランデューサー部分をよりよくするための研究やその生産体制強化を行っていきたいと考えています。 まだまだ進化できる部分であり、そこが魅力的なところです。
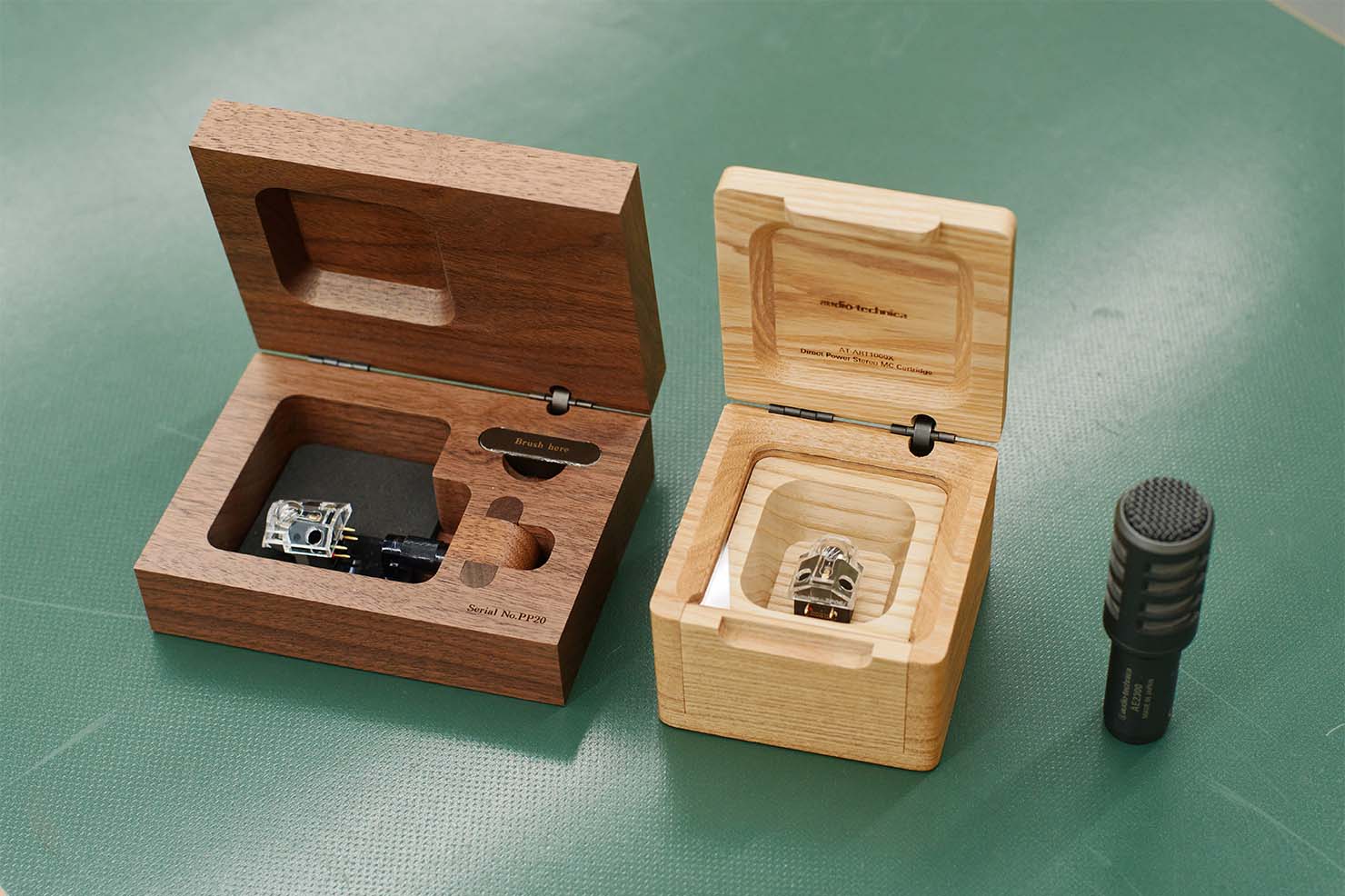
最後に、ART1000Xでのリスニングを楽しむのにおすすめのレコードを1枚、教えてください。
『AUTUMN LEAVES』という MANHATTAN JAZZ QUINTETのレコードです。 特にA面1曲目と3曲目が個人的にカートリッジによる変化が分かりやすく、1曲目のサックスと両曲の終盤が聴き比べをするときに楽しいです。
ART1000Xではより低域表現が増したので、違いが映えるのではと思っています。
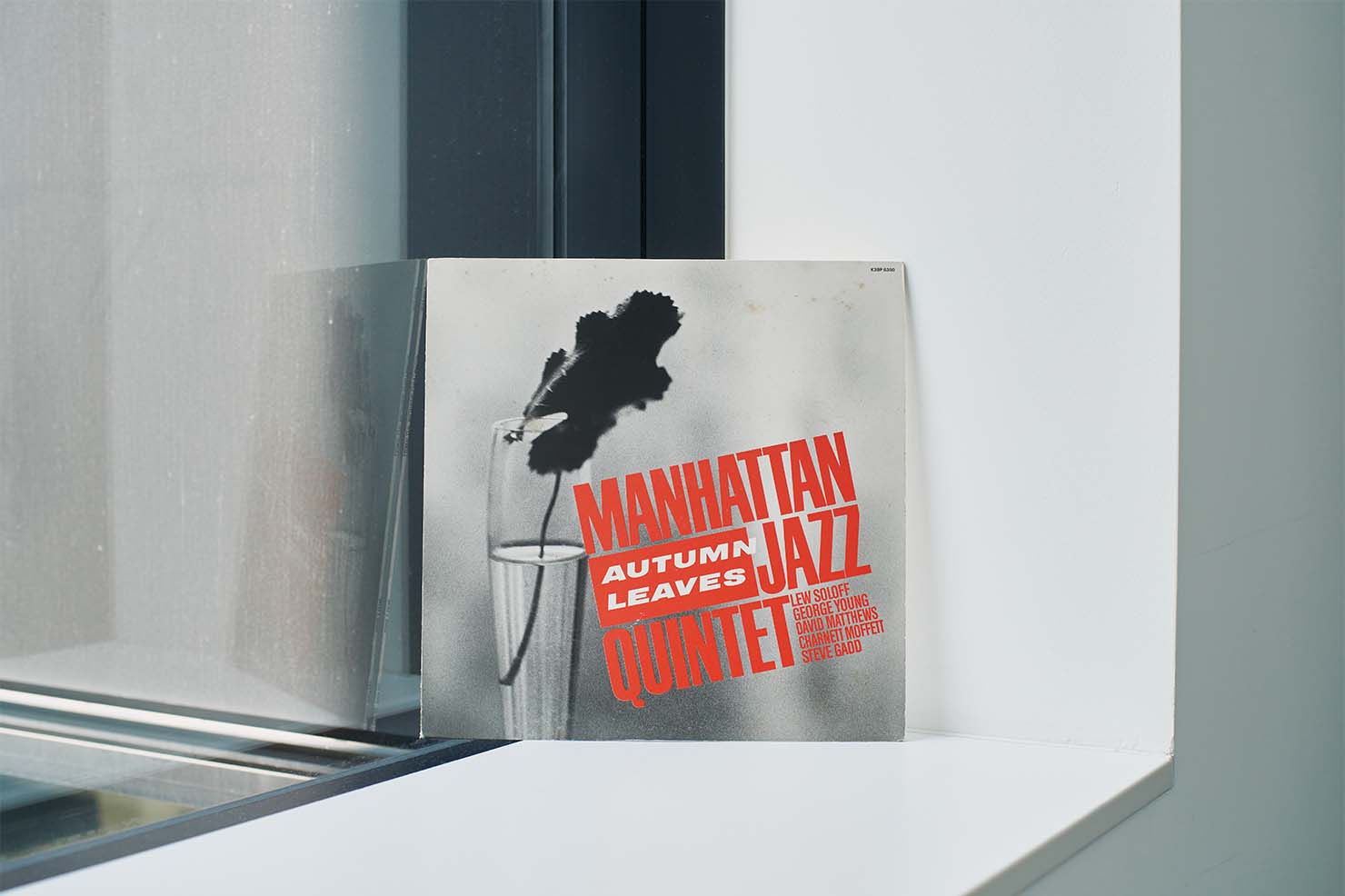
エンジニア 髙橋さんのとある1日
8:15 | 出勤 |
---|---|
8:35 | 業務開始 納品管理、生産業務(組立)、生産改善業務(生産ラインのレイアウト変更など) |
12:15 | ランチ 食堂で昼食を食べたり、音楽を聴いたりしていることが多い |
13:00 | 午後業務スタート 生産業務(組立)、生産改善業務(不良品の原因解析など)、打ち合わせ |
17:20 | 業務終了、退勤 |
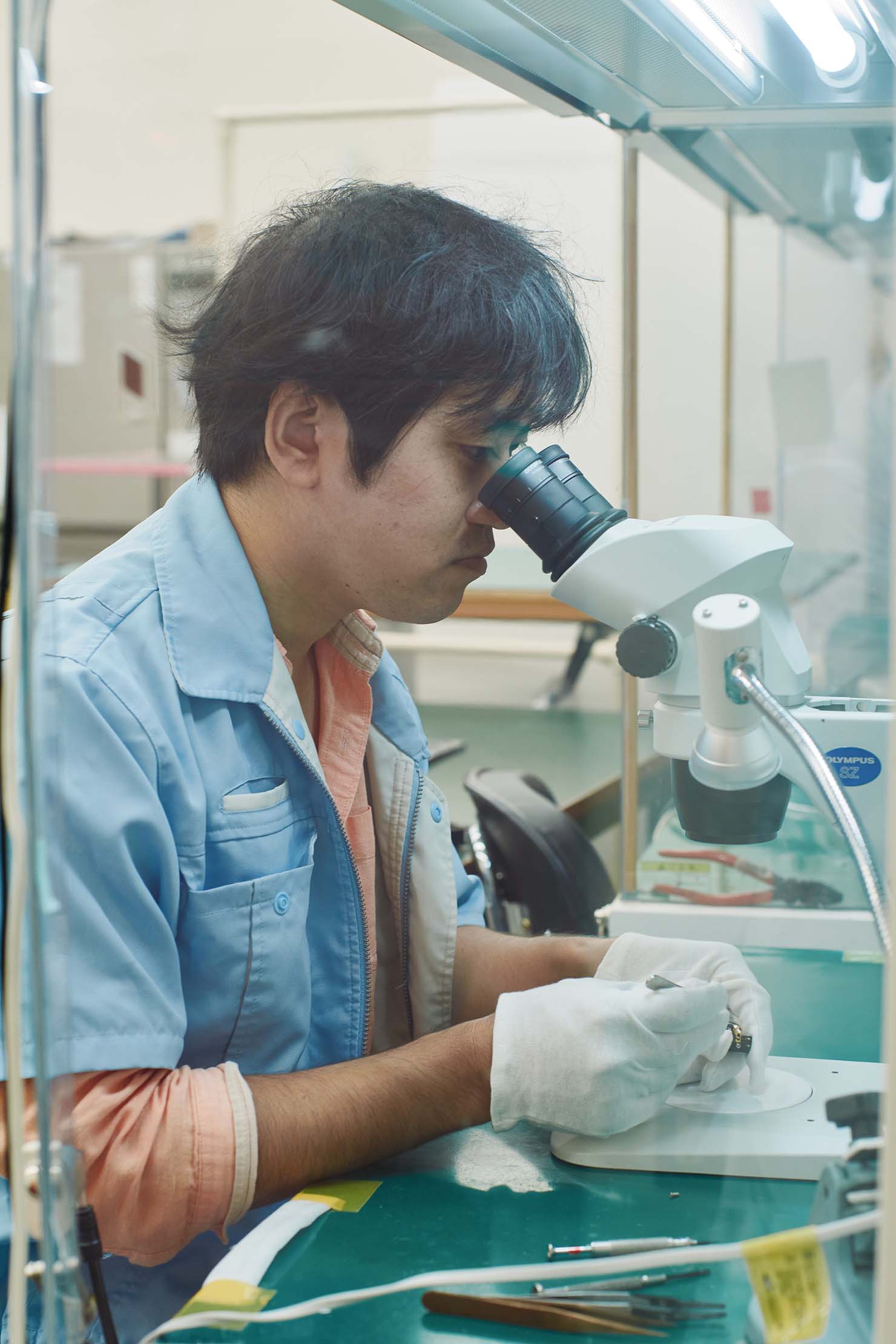
Engineer:Yuzuru Takahashi
Photos:Hinano Kimoto
Edit:May Mochizuki
Direction:E.SUKIKO